Torquing and hydraulic tensioning are two key methods for tightening bolts, each with its own benefits. Learn how to choose the right approach for better joint reliability and safety.
Torquing is the traditional method of tightening bolted joints, and it’s one of the most widely used techniques because of its simplicity. Whether done manually or by using mechanical tools, it’s quite straightforward.
You can achieve controlled tightening with just one torque wrench and a range of sockets, which is why it’s so cost-effective and flexible. It’s easy to train someone to use it, and it can handle a broad spectrum of bolt sizes.
However, it’s essential to keep in mind that although it’s a simple method, there are technical aspects to consider, especially in applications that require precise torque.
For example, friction can often become the primary challenge when tightening with torque. In many cases, up to 90% of the torque applied goes into overcoming friction, which means only a small portion of that torque is actually used to create the bolt load. These friction losses are one of the key challenges faced when it comes to achieving precise bolt loads.
Other parameters that affect achieving bolt loads are the type of lubricant used, the condition of the bolt and nut threads, the atmospheric conditions, the grade of bolt used, condition of joint, preparation of joints etc.
Achieving a consistent bolt load is more important than hitting the target torque. For example, a flange may leak even if the target torque is achieved when the flange preparation is not done as per the procedures, sequence and bolting patterns are not followed etc.
The tool may achieve its final set torque, but the flange would still end up failing if the above procedures are not followed. Bolt Load consistency should be the final goal.
Hydraulic tensioning, and why has it gained traction in certain industries?
Hydraulic tensioning started gaining popularity in the 1970s, and it’s becoming the preferred method for certain high-stakes applications. Unlike torquing, tensioning directly stretches the bolt using hydraulic force. This eliminates the load losses caused by Friction and Bolt conditions.
In applications like oil and gas, power generation, and subsea industries, the bolt sizes goes up to 7”, hydraulic tensioning provides greater consistency than torque. The ability to control the load on the bolt and achieve uniform clamping across multiple bolts simultaneously makes it ideal for complex flange joints.
As I explored the differences between torquing and tensioning, I reached out to Sandeep, an expert in bolting solutions, to get his insights. Our conversation shed light on the advantages, challenges, and key considerations for choosing the right method.
Simran: So, hydraulic tensioning seems to offer more control and consistency. However, is it a more complex and expensive process?
Sandeep: Yes, that’s true. Hydraulic tensioning requires more specialized tools, such as tensioners with their respective adapter kits, making the process comparatively more expensive. It’s also a more complex procedure. The tensioners are designed to apply the exact amount of load needed to achieve a certain bolt tension.
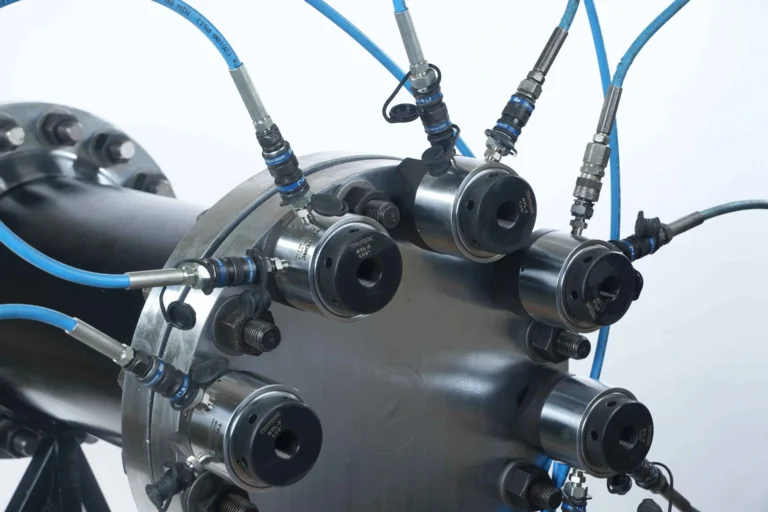
One of the advantages is that you can tighten multiple bolts simultaneously, ensuring even compression of the gasket or flange. This helps prevent uneven loading, which could cause issues with the joint integrity.
But, the complexity and the cost of the equipment involved are significant drawbacks when compared to simpler torquing methods.
Simran: That’s interesting. You’ve touched on consistency a few times now. Can you explain a bit more about why tensioning is more consistent in some cases, and why not all bolts are suited for it?
Sandeep: Hydraulic tensioning tends to be more consistent when you’re dealing with long bolts or situations where very high bolt loads are required. In these cases, tensioning provides more precise control over the standard torque tightening.
However, tensioning may not be as effective on short bolts or applications where lower bolt loads are needed. In these instances, the tensioning process might lose some of its accuracy due to the physical nature of the bolts. It’s all about the bolt geometry and the load requirements—tensioning excels when the conditions align.
Simran: And are there any other challenges with hydraulic tensioning?
Sandeep: Yes, there are a couple of practical concerns. One key challenge is Load Transfer and load bounce. When the tensioner is released, the load is transferred to the nut, which can cause a reduction in the overall load.
To overcome this Load Transfer, it is paramount to understand if the load provided by the user is Applied Load or Residual Load.
Another practical issue is the complexity of the tools required. Since tensioning tools are more specialized, it’s harder to match a single set of tools to a variety of different bolts, unlike the more flexible torque wrenches. The logistical and physical constraints, such as space limitations or the need for specific tooling, also add to the complexity.
Simran: It seems like the decision between torquing and tensioning isn’t straightforward. How should someone decide which method to use?
Sandeep: The choice really depends on the specifics of the joint and the application and the requirements of the engineering team. Some OEM’s would prefer torque tightening and other OEM’s prefer tensioning. However, a lot of OEM’s prefer both Torque tightening and Tensioning.
Industries like Wind Turbines, Heat Exchanger manufacturers carry out torque tightening and tensioning both on their applications.
You also need to think about the tools and equipment available, the location of the joint, and the personnel on site. It’s important to weigh the technical requirements alongside the practical constraints. And, as always, the goal is to ensure a safe, effective, and reliable joint under all operating conditions.
Simran: Sandeep, thank you for your insights. It’s clear that both methods have their place, depending on the application, and it’s important to assess each situation individually.
Sandeep: My pleasure, Simran. Exactly, there’s no universal solution. It’s all about understanding the application and making an informed decision to ensure the joint performs optimally.
Conclusion
Wrapping up our discussion, I want to thank Sandeep for sharing his expertise on bolting solutions.
Both torquing and tensioning have their advantages and limitations, and choosing the right method depends on the application’s requirements. While tensioning offers precision and consistency, torquing remains a cost-effective and flexible solution. The key is to evaluate each joint carefully to ensure safety and reliability.
Leave a Reply