Oil and gas is at a crossroad right now because of the growing demand, new technology, and the environmental pressures that will eventually change the face of operations. One of the biggest issues is still that of effective maintenance, specifically the avoidance of forced outages, the extension of asset life, and the upholding of high operational safety. The face of oil and gas maintenance will change dramatically in the future, and Tritorc will lead the way in developing new ways to overcome some of the problems associated with maintenance.
Current and Future Challenges in Oil and Gas Maintenance
1. Aging Infrastructure
Much of the world’s oil and gas infrastructure is old; many of the facilities are operating well past their expected life. That raises many problems, such as corrosion, mechanical wear, and growing maintenance expenses. Old infrastructure is susceptible to failures that could result in disastrous shutdowns and contamination hazards.
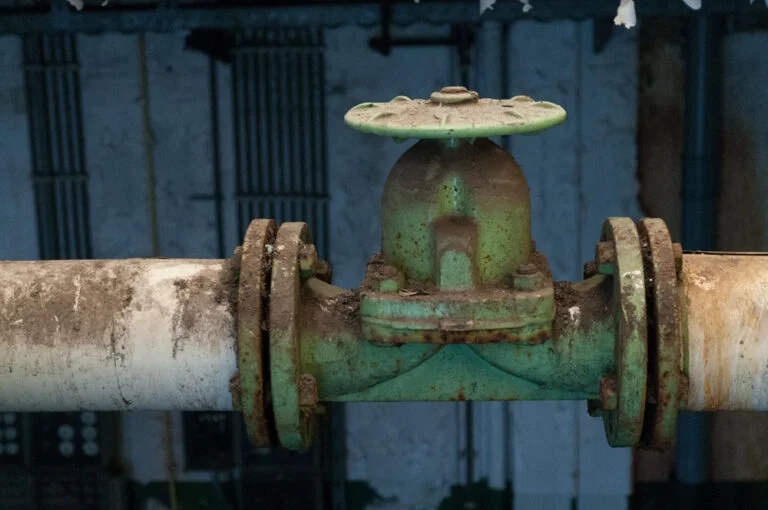
Tritorc Solution: Tritorc offers the well-engineered hydraulic torque wrenches and bolt tensioners on the market, which offer the accuracy needed in heavy-duty bolting applications so that old equipment can be kept up to the highest standards. Tritorc’s bolting tools ensure joint integrity against flange leaks, structural instability, and other maintenance failures due to aging equipment by precisely tightening critical components.
2. High Maintenance Costs
A large part of the operating expenses in the oil and gas business are maintenance costs. The labor and machine downtime and material cost to replace add up pretty fast, and then there’s always the chance that the failure of one part will cause a chain reaction with other parts, which will in turn cause more failures, and that chain reaction can cause catastrophic failures throughout the supply chain.
Tritorc Solution: Tritorc’s hydraulic flange spreaders and bolt tensioning systems make flange management woes a thing of the past, and without the human error and downtime waiting for repairs. Our hydraulic tools allow for efficient work with less manpower, less maintenance cost, and little to no downtime.
3. Unscheduled Downtime
Well, unplanned downtime in oil and gas operations not only costs money but also risks the safety of the workers and possibly environmental compliance. Predictive maintenance is being used to cut down on unplanned downtime; however, these methods require high-precision tools to implement.
Tritorc Solution: Our pipe-cutting and bevelling machines allow for quick, precise repairs, minimizing downtime during critical shutdowns. Tritorde’s equipment is made for extreme usage and can cut repair time by over 40%, but our bolt tensioning systems can guarantee no leaks when bringing the unit back online, thus reducing risk and downtime.
4. Skilled Labor Shortages
As oil and gas operations become more complex, lack of skilled labor is a serious issue. Maintenance procedures need to be done by experienced hands, and if there is any break in that chain, it can become very expensive in inefficiencies, not to mention safety problems.
Tritorc Solution: Tritorc’s bolting tools and machines are very easy to use, and they don’t require much training. Our methods include automation so that there is little need for highly skilled labor, but the results are extremely accurate. From bolt tensioning to pipe beveling, the ergonomically designed equipment cuts down on training time and increases worker productivity.
Tritorc’s Bolting and Maintenance Solutions
Hydraulic Torque Wrenches: These tools provide accurate torque control for bolting applications, with torque outputs as high as 80,000 ft-lbs, to ensure leak-tight performance in vital high-pressure situations.
Hydraulic Bolt Tensioners: Tritorc’s tensioners provide even bolt preload over a number of bolts in a joint, making it much safer and also increasing the life of the equipment.
Flange Facing Machines: Tritorc’s flange facing machines can resurface flange faces up to 120 inches in diameter, leaving a perfect surface finish and eliminating the possibility of leaks in high-pressure systems.
Pipe Cutting and Bevelling Machines: The cold-cutting machines made by Tritorc are designed for larger diameter pipes and allow for quick, precise, and safe cuts with minimal heat-affected zones.
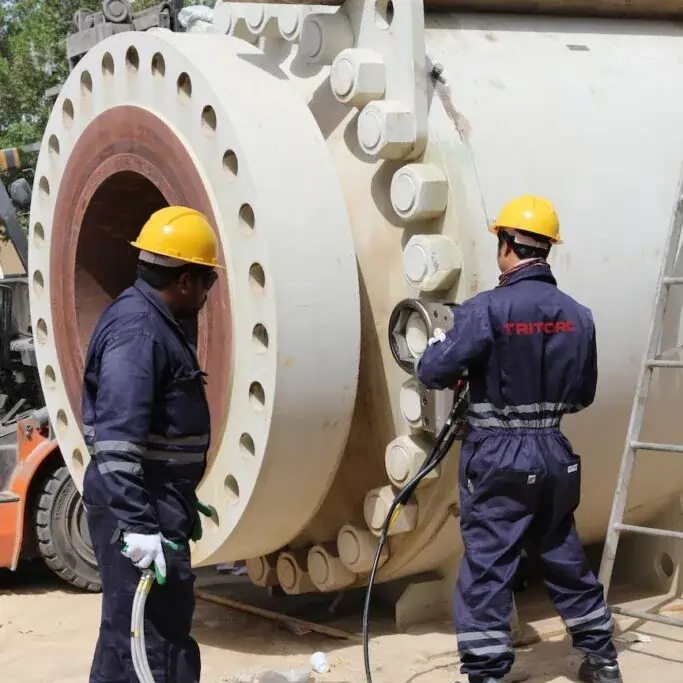
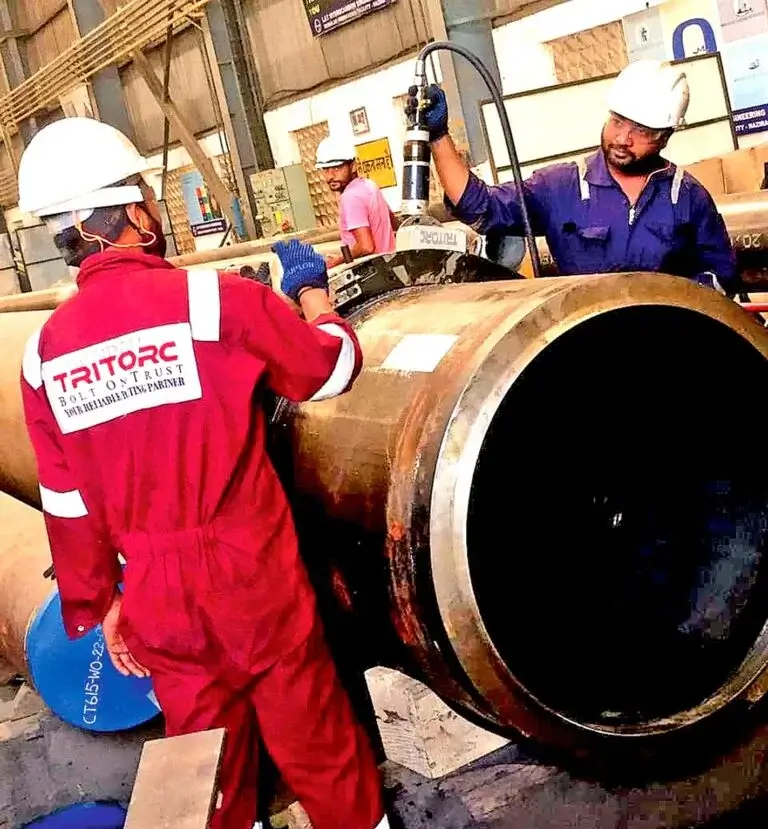
Looking Ahead: Proactive Maintenance in Oil and Gas
In the oil and gas industry, the trend is going to PdM and proactive maintenance. Nowadays, predictive maintenance technologies, whether they be real-time monitoring systems or AI-driven analytics, are vital in order to predict when a piece of equipment will fail before it does. But all of these strategies are worthless if the maintenance tools are not there to support them.
Tritorc’s new solutions are poised to enable the future of predictive maintenance. Through the combination of our highly accurate bolting and machining tools with modern data-based systems, we can assist companies in eliminating their downtime, cutting back their operational costs, and improving the safety and life of their vital equipment.
Leave a Reply