Continuous operating stresses, exposure to the environment, incorrect installation, and material wear can cause degradation of flanges. Not addressing the damage early can lead to serious safety risks, expensive downtime, and significant repairs.
In order to have safe operational productivity and adherence to industry norms like ASME B16.5, ASME B16.47, and ANSI/ASME PCC-1, periodic inspection of flange assemblies is mandatory. The procedure involves assessing the flange face, gaskets, bolt alignment, parallelism, corrosion levels, stress cracking, and mechanical damage.
A thorough inspection helps to identify possible issues before they become major failures. In the following blog, we will discuss the most important technical indicators pointing toward a need for maintenance on a flange.
Surface Irregularity and Flange Face Condition
The integrity of the flange face is an important factor in having a leak-proof and secured seal. A defective or uneven flange face may result in improper gasket seating, which could lead to leakage of fluid or gas. The most common flange face defects include pitting, corrosion, grooving, warping, and scratches.
Pitting and Corrosion
Exposure to aggressive chemicals, fluids, and extreme temperatures is known to result in pitting corrosion on the surface of the flange. Pitting forms localized depressions that cause difficulty in uniform seal formation by the gasket. Corrosion may result in material thinning, making the overall flange strength weaker.
Grooving and Erosion
High-velocity fluid flow, abrasive particles, and tough conditions can gradually wear out the flange surface that creates grooves and compromise gasket effectiveness. Grooves alter the sealing surface and increase the likelihood of leaks.
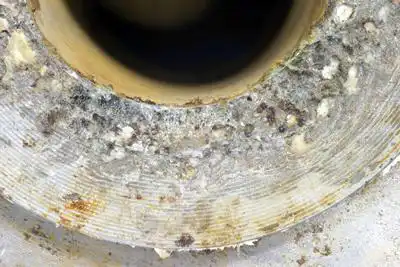
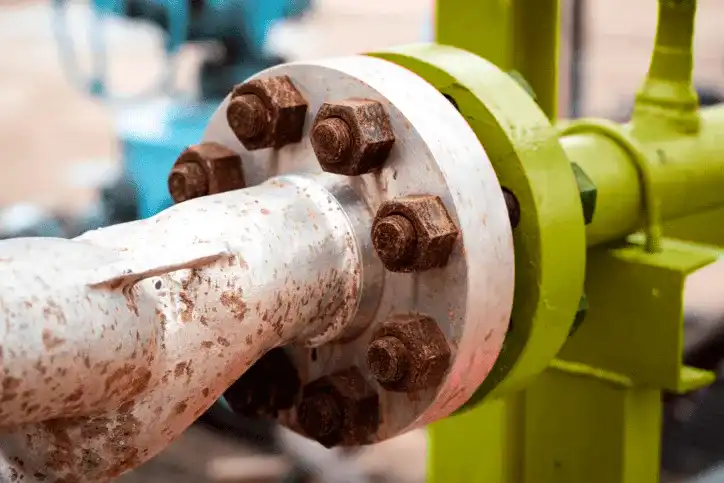
Warping or Deformation
When excessive bolt loads or improper tightening sequences are applied, the flange face may warp or get distorted. A warped flange will not mate properly with the opposing flange and will either lead to uneven gasket compression or create leak paths.
Scratches and Mechanical Damage
Poor handling, impact during installation, and incorrect gasket removal can leave scratches or may create indentations on the flange face. A slight surface imperfection can interfere with the gasket’s ability to maintain a tight seal, or you will have to look for a flange replacement.
Gasket Condition and Sealing
Gaskets serve as a vital barrier in the bolted flange joint by occupying the surface irregularities and avoiding fluid or gas leakage. Gaskets wear out over time because of thermal expansion, chemical attack, and mechanical stressing. Common gasket failures that indicate the need for flange maintenance include:
Gasket Blowout
Blowouts of a gasket occur due to excessive pressure, incorrect gasket selection, or insufficient bolt torque. A sudden rupture or displacement of the gasket can result in significant leakage and safety hazards.
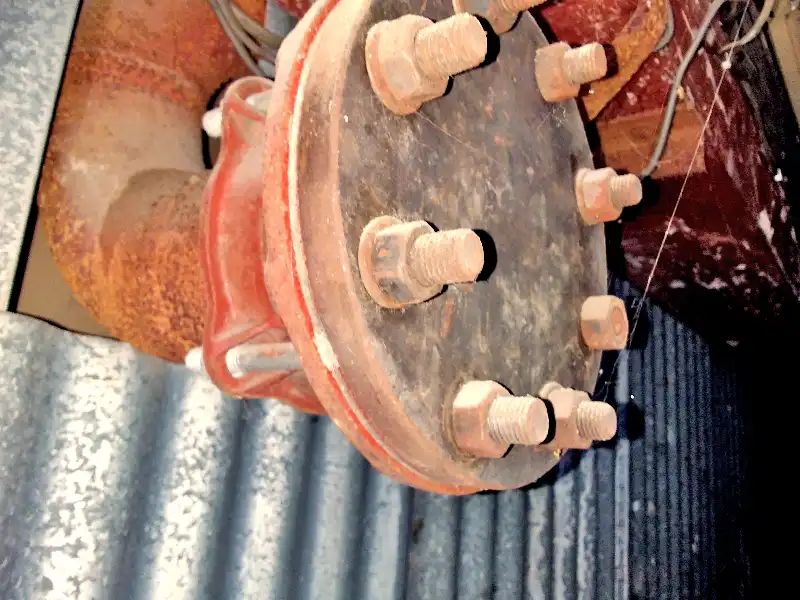
Creep Relaxation
Creep refers to the long-term deformation in gaskets from being under a constant load.
Soft gaskets, particularly rubber gaskets, sometimes undergo creep over time, which leads to loss of sealing stress. This results in loosening of the bolted connection and eventual leakage.
Improper Compression
Over-tightening a gasket can cause crushing and extrusion beyond its optimum dimensions. On the other hand, under-tightened gaskets may not provide enough surface contact, which again causes leaks.
Chemical and Thermal Degradation
Continuous exposure to harsh chemicals, high temperatures, and fluctuating pressures can degrade gaskets. Some materials, such as rubber and elastomers, may harden, shrink, or become brittle over time due to temperature or chemical exposure.
Bolt and Fastener Check
The integrity of the bolting assembly is critical to ensure and secure flange connection. Problems with bolts, nuts, and washers can jeopardize the entire flange joint, resulting in gasket failure and the joint’s loosening. Factors that require monitoring:
Bolt Stretching and Yielding
Excessive preload or prolonged operational stress may permanently stretch bolts beyond their elastic limit. A stretched bolt loses its ability to maintain proper clamping force and reduces flange joint reliability.
Loose or Uneven Bolt Tightening
Failure to follow a proper tightening sequence can result in uneven gasket compression. This can create random weak points and allow leaks to develop over time.
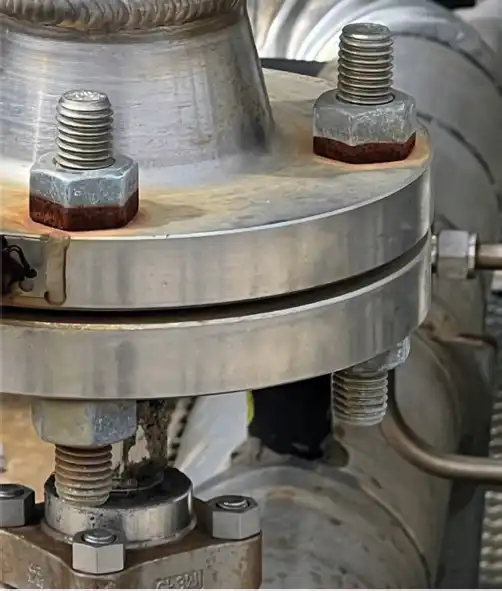
Corrosion and Galling
Bolts exposed to corrosive environments and used in industries such as offshore and chemical processing can progressively worsen. Galling, a common phenomenon in stainless steel fasteners, may lead to material adhesion between the bolt and nut, making future maintenance difficult.
Thread Damage and Wear
Damaged or worn threads on bolts and nuts reduce the effectiveness of torque application and clamping force. These occur when the nuts and bolts are not handled properly. Threads should be inspected for signs of stripping, galling, or deformation before installation.
Bolt Hole Alignment Issues
Misaligned bolt holes can introduce stress concentration points, which makes it difficult to achieve uniform bolt loading. Even misalignment causes damage to the gaskets. Ensuring precise alignment of the bolt and nuts during installation is critical to maintaining the integrity of the flange connection.
Flange Alignment Issues
Misalignment while mating flanges can cause gasket over-compression on one side and under-compression on the other. Common alignment problems include:
Angular Misalignment
When flanges are not perfectly parallel, one side experiences excessive stress which causes an uneven sealing surface. This condition often occurs due to pipe misalignment or improper welding procedures.
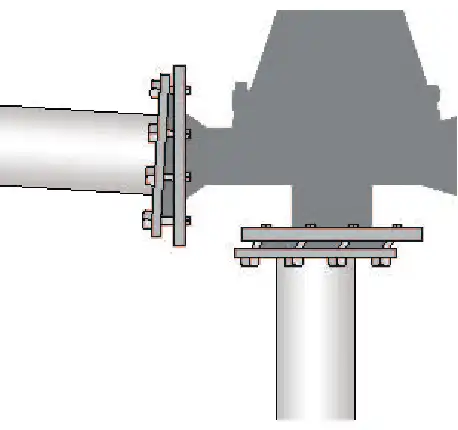
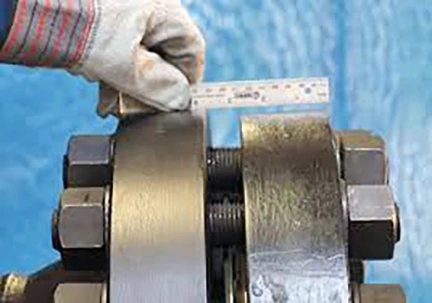
Radial Misalignment
If one flange is not centered properly with respect to the other, the bolt holes may not line up correctly. This condition can lead to bolting strain and structural weaknesses within the joint.
Flange Rotation and Pipe Strain
External pipe stresses, improper support, or excessive force during installation can cause flanges to rotate, misalign, and cause additional stress on bolts and gaskets.
Structural Damage and Stress Cracking
Flanges experiencing cyclic loading, thermal expansion, and vibration can develop micro-cracks and structural defects. These issues may not be visible immediately but can lead to catastrophic failures if left unaddressed.
Stress Corrosion Cracking (SCC)
Corrosion that occurs when a material is subjected to both tensile stress and a corrosive environment. Stainless steel and high-strength alloys can cause SCC when exposed to chlorides or other harsh substances. Fine cracks in the flange get weakened and make it prone to sudden failure.
Brittle Fracture
Sudden and rapid cracking of a material under stress, with minimal or no plastic deformation, surfaces often appear flat, shiny, and may exhibit cleavage facets. This phenomenon is particularly common in carbon steel flanges that do not possess sufficient impact resistance.
Flange Bulging and Distortion
Excessive bolt torque or fluctuating pressure conditions can cause the flange to bulge, deforming the flange and altering the space for the gasket.
Non-Destructive Testing (NDT) Methods
Use advanced inspection techniques to find flange flaws that are invisible to the human eye.
Ultrasonic Thickness Testing (UTT)
Determines if the flange material has thinned due to corrosion or erosion.
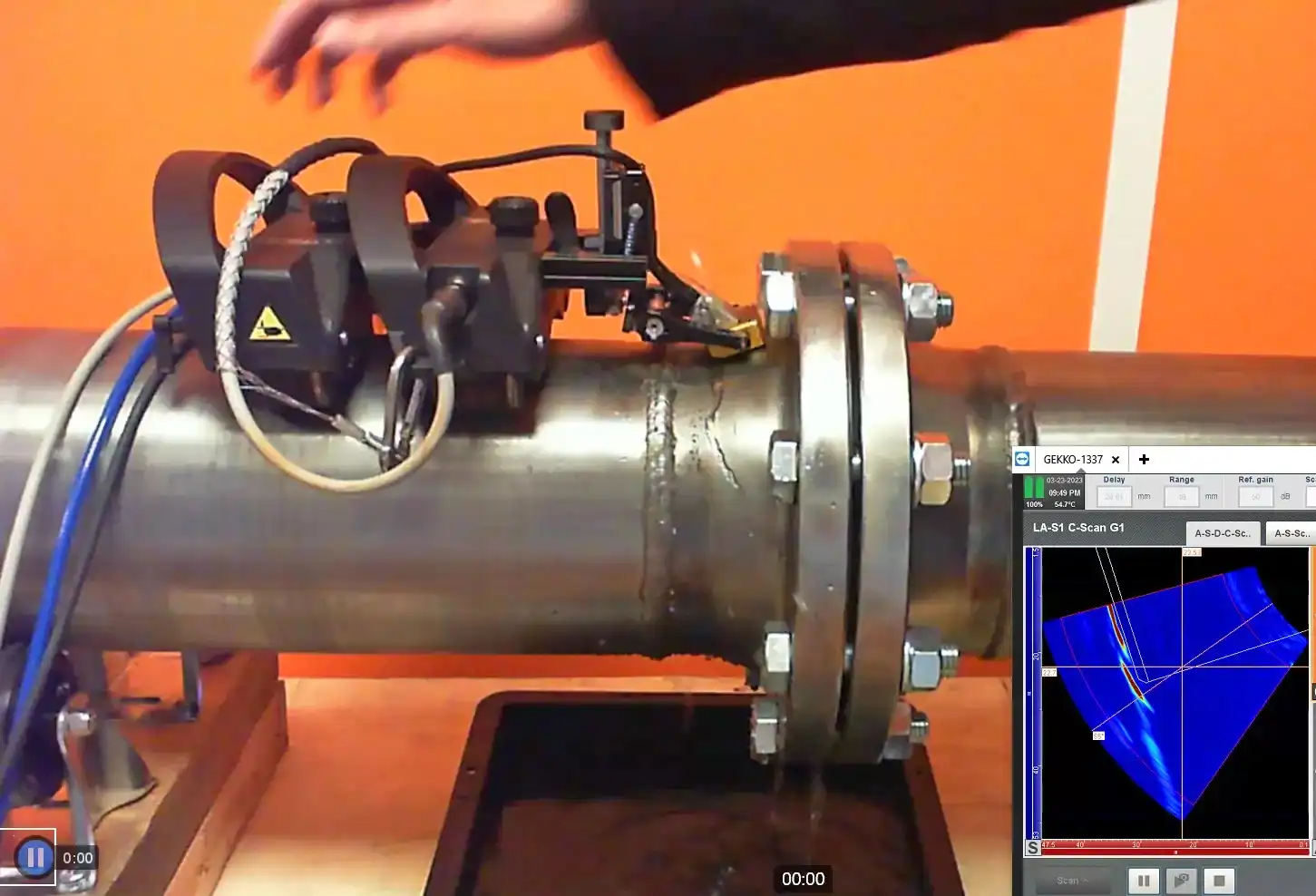
Magnetic Particle Inspection (MPI)
The device detects surface and near-surface cracks in ferromagnetic materials.
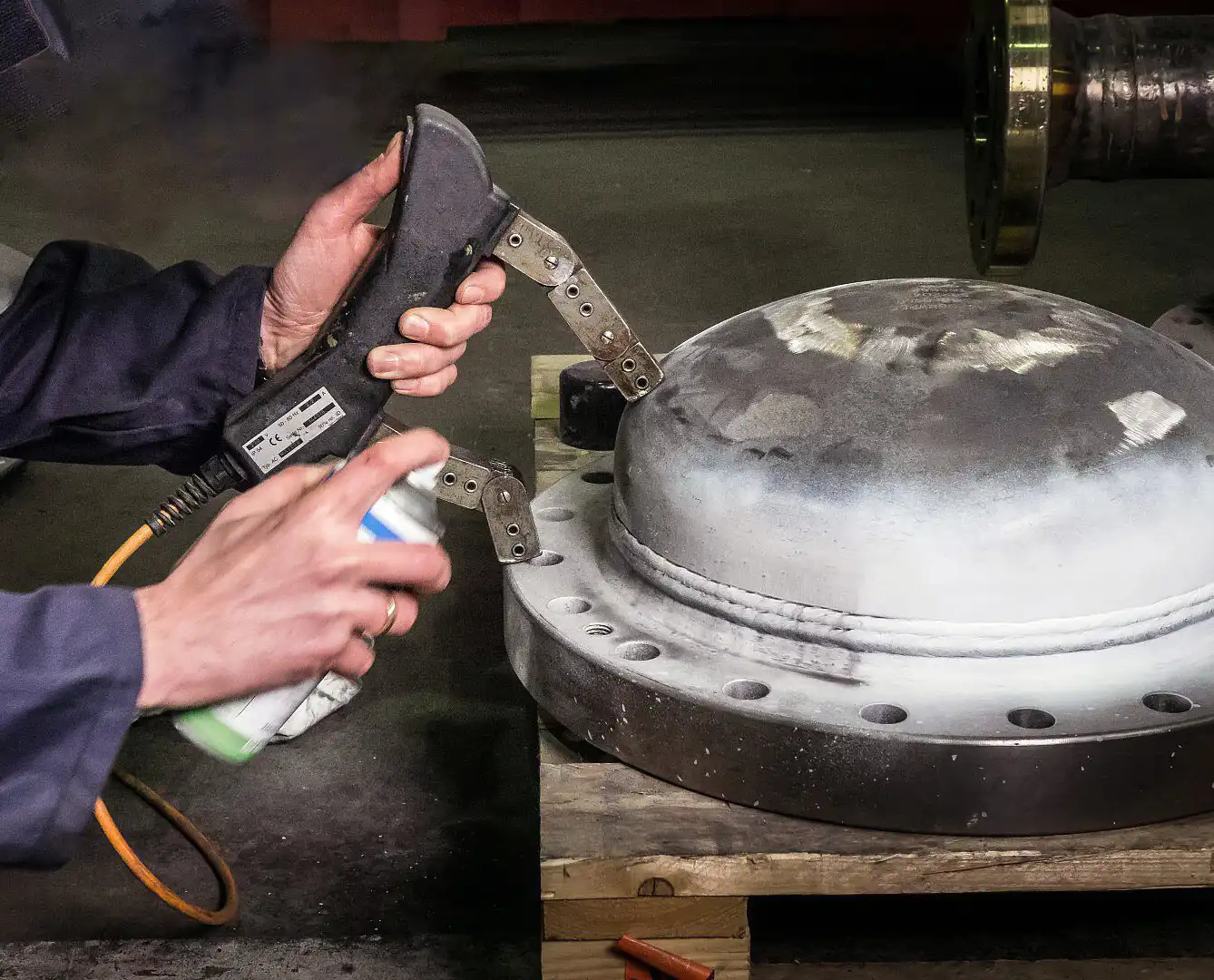
Dye Penetrant Inspection (DPI)
Highlights fine cracks and defects in non-ferrous flanges.

Radiographic Testing (RT)
The process uses X-ray imaging to identify internal porosity, voids, and inclusions.
Conclusion
Knowing early warning signs like misalignment, corrosion, mechanical damage, and stress cracking enables easy maintenance and reduces the chances of surprise failures.
Adherence to standards like ASME B16.5, ASME B16.47, and ANSI/ASME PCC-1 assures that flange assemblies are secure and functional. For an insight into the major causes of flange damage and prevention of the same, refer to our detailed blog on Common Causes of Flange Damage.
Leave a Reply