Tritorc secured a challenging offshore hot tapping project from one of the largest MNCs in the world through a strategic and collaborative approach. Leveraging strong industry reputation and expertise in hot tapping solutions, Tritorc engaged proactively with the client’s procurement and engineering team.
Introduction:
The hot tapping project at an offshore process platform aimed to create a new 8-inch connection on an existing 12-inch pipeline to facilitate process expansion. This execution was carried out in the 1st and 2nd week of April 2024. The need for the hot tapping project arose from the client’s requirement to expand their process capabilities while ensuring minimal disruption to ongoing operations. The platform, located in the Northern oil field in the Indian Ocean, required a reliable and efficient solution to accommodate the expansion.
Project Objectives:
- Design and implement a hot tap fitting in accordance with ASME B31.3 standards.
- Select suitable split tee material as per MSS SP standards.
- Fulfill Quality Assurance Plan (QAP) and Inspection Test Plan (ITP) for split tee fabrication.
- Modify equipment to suit H2S presence and conduct pre-mobilization testing.
- Perform on-site in-service welding with controlled parameters as per API 1104 Appendix B.
- Execute the hot tapping operation safely in compliance with API 2201 standards.
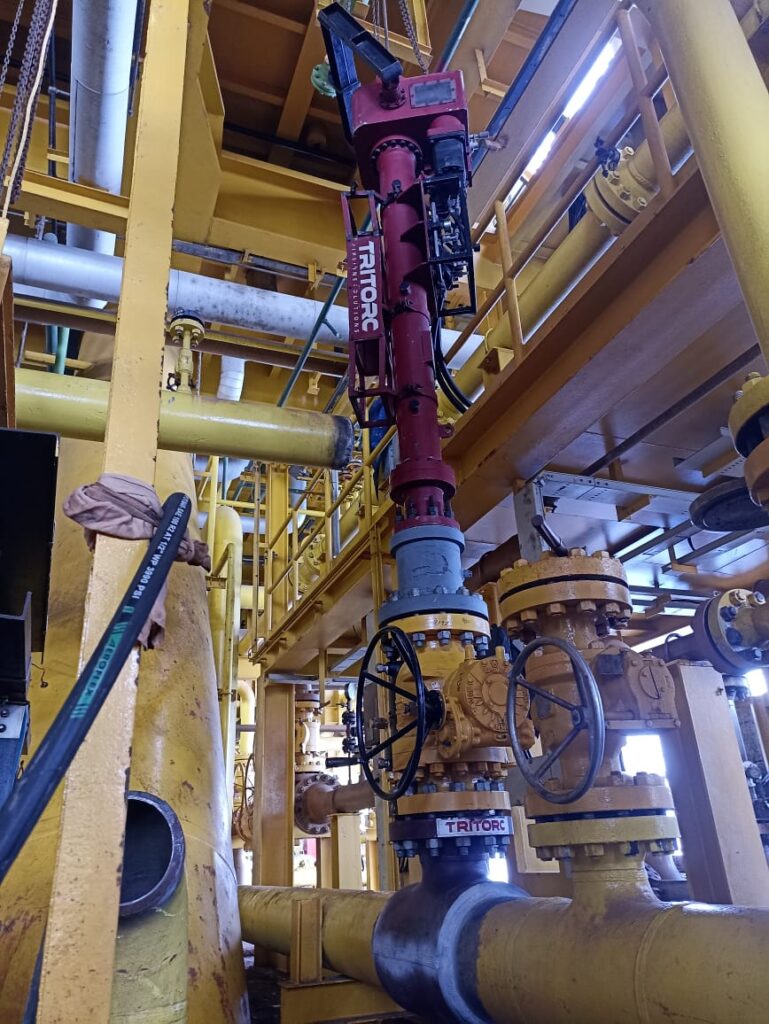
The project involved meticulous planning, including site selection, safety assessments, and equipment procurement. Tritorc deployed specialized hot tapping equipment modified for H2S environments.Exposure to H2S poses significant environment and safety concerns. Given the presence of corrosive gas, Tritorc addressed environmental concerns by implementing ventilation systems, providing appropriate personal protective equipment, conducting risk assessments, monitoring H2S levels, and complying with environmental regulations. The hot tapping procedure followed industry standards and incorporated innovative techniques to ensure precision and safety.
Quality Control checks and Inspections:
1. Before the mobilization of the split tee, all non-destructive testing (NDT) tests were carried out as per the ASME Section V standards to ensure the integrity of the equipment and materials.
2. During the split tee welding process, dye penetrant testing (DPT) was conducted for root welding, and all subsequent passes underwent magnetic particle inspection (MPI) to detect any potential defects or imperfections in the welds.
3. Additionally, a function leak test was performed according to API 2201 standards before the hot tapping process to verify the integrity of the connections and to ensure there were no leaks present before proceeding further with the operation. These checks and inspections help maintain high-quality standards and ensure the safety and reliability of the equipment and operations.
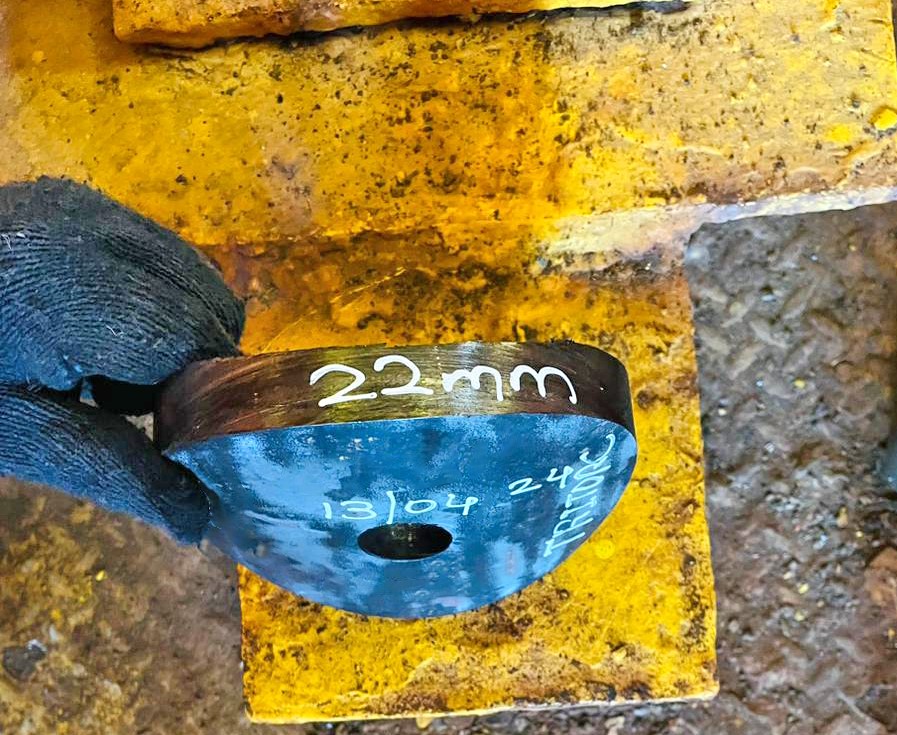
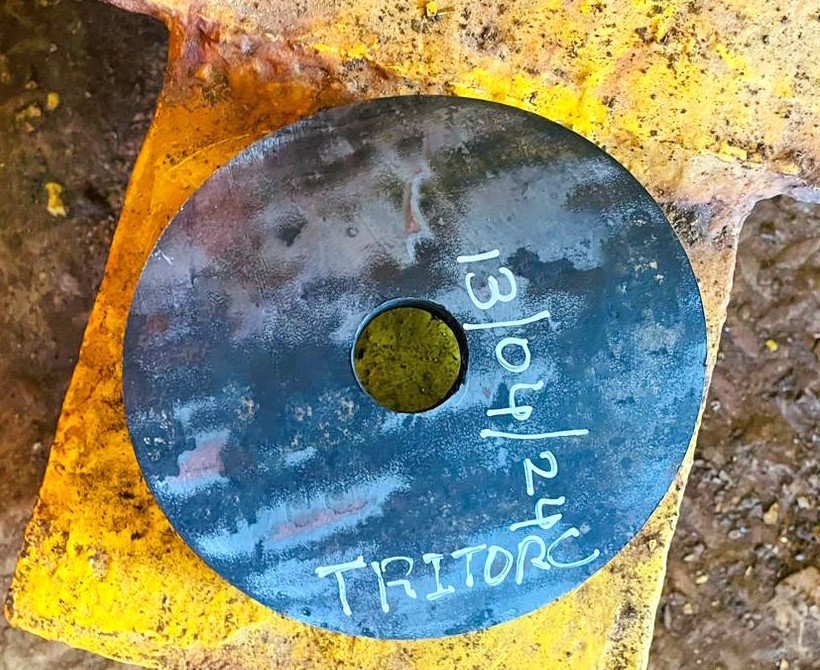
Challenges Faced and Solutions Implemented:
Challenges such as equipment availability, suitability, and offshore logistics were addressed through careful planning and collaboration with suppliers. The team implemented innovative approaches, including pressure-balancing hot tapping machines and inconel fasteners, to overcome operational constraints. Heavy tools and equipment for hot tapping were transported to the offshore site via supply vessels.
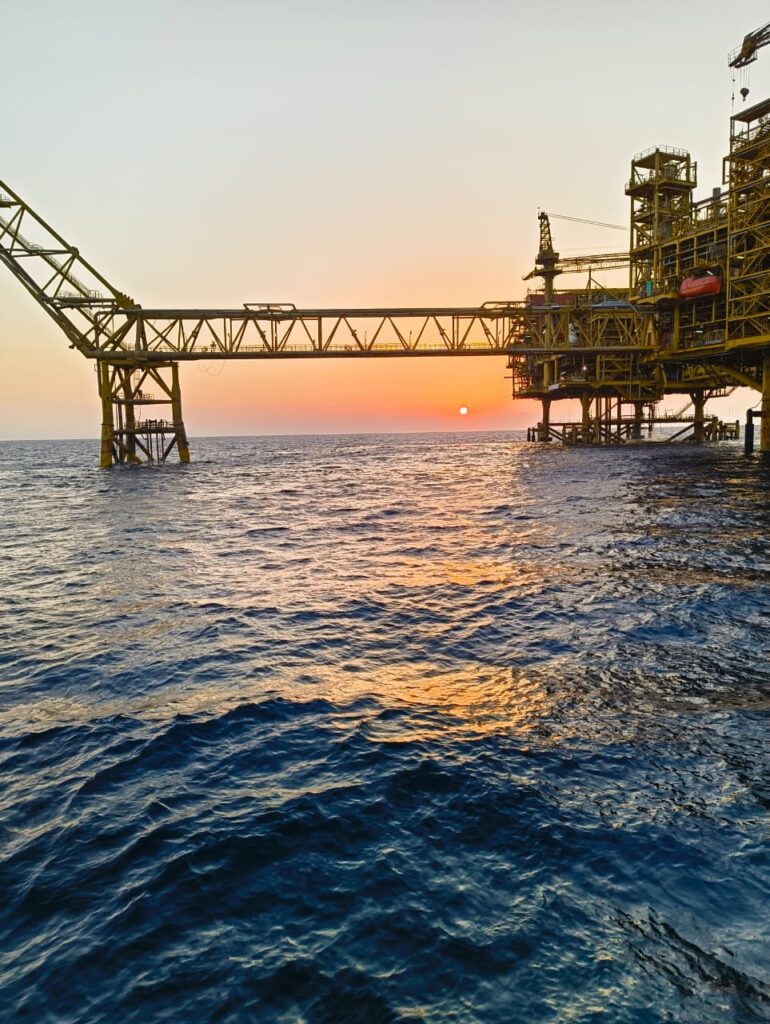
Results and Outcomes:
The hot tapping operation was executed successfully, achieving all project objectives. Quality control checks and inspections were conducted throughout the process to maintain high standards. The operation was completed within the scheduled timeline and budget, demonstrating expertise and efficiency.
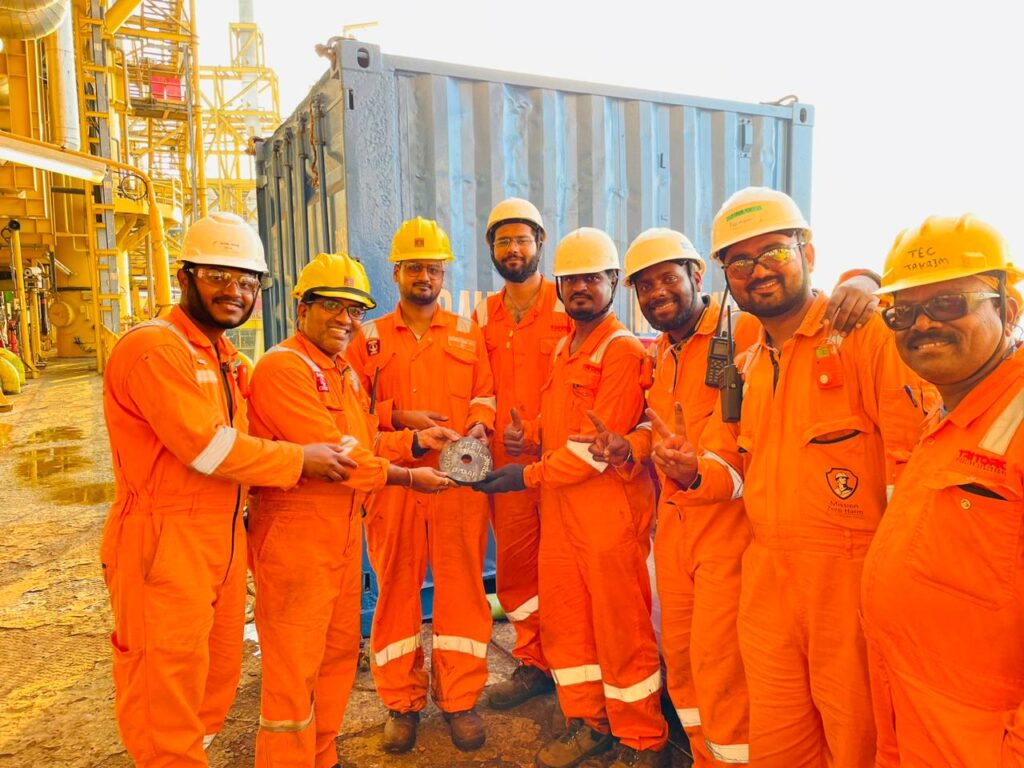
Key Takeaways:
Key takeaways from the project include the importance of specialized equipment, rigorous safety protocols, and continuous quality control. Recommendations for future projects include the use of advanced cutting tools, pressure-balancing machines, and high-quality fasteners to enhance efficiency and reliability.
Conclusion:
The hot tapping project at the offshore Process Platform showcased Tritorc’s commitment to delivering innovative solutions while prioritizing safety and quality.
Leave a Reply