Introduction:
To understand this blog better, have a look at our earlier introductory blog on this topic…
As seen in our earlier article the hot tapping process involves the installation of a valve onto the existing pipeline while it is in operation. Hot tapping, also known as pressure tapping, is a technique used to connect a new branch pipeline to an existing pressurized pipeline without interrupting the flow of the fluid or gas. This method is commonly used in industries such as oil and gas, water supply, and chemical plants to increase efficiency and reduce downtime.
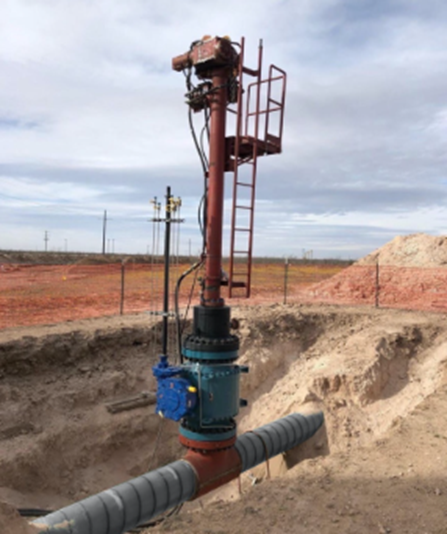
To explain the process in brief:
A Hot Tap fitting such as an RF Pad, Weld-O-Let, or Split Tee is bolted or welded (mostly welded) on the target pipeline, known as the Mother pipeline. A full bore Gate Valve is mounted with seals and tightened with bolts. A hot tapping machine is then mounted on the valve.
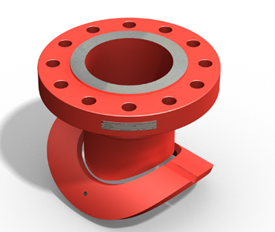
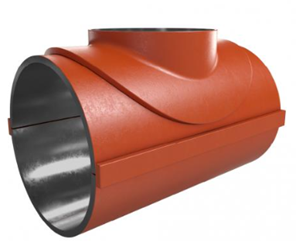
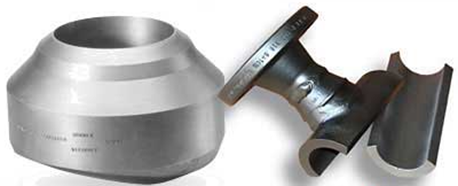

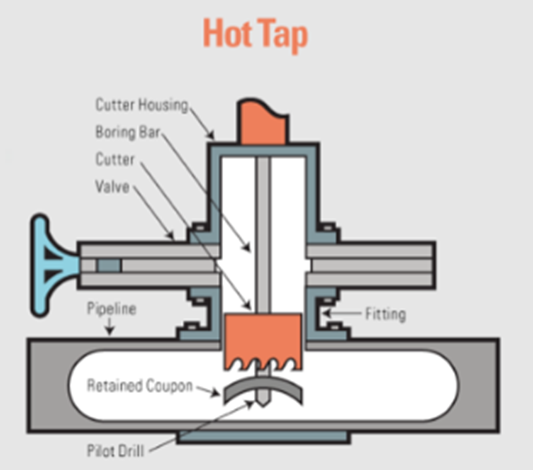
The Hot tapping machine is operated, The Pilot Drill is the first to make contact with the pipe surface followed by the cutter. This step is followed by the extraction of the coupon. This completes the hot-tapping process.
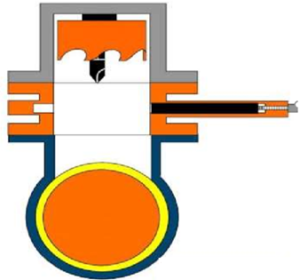
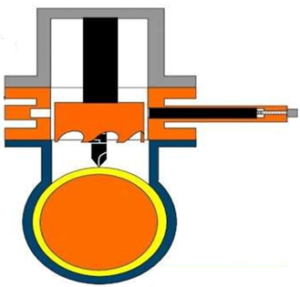
till it touches pipe and then cutter is started
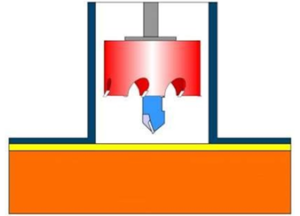
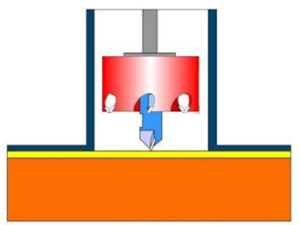
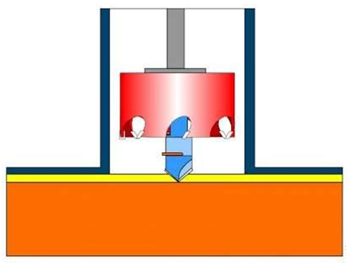
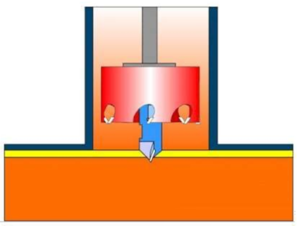
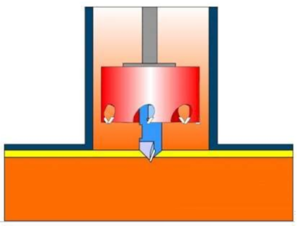
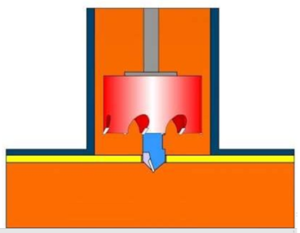
When the Pilot Drill Breaks through the pipe, the product/ fluid fills the void. Air is expelled through the tapping machine purge valve. Following this the valve is closed to retain the pressure.
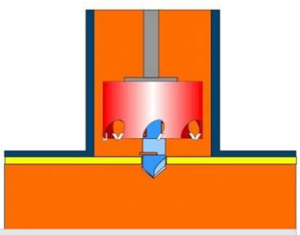
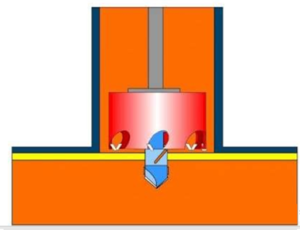
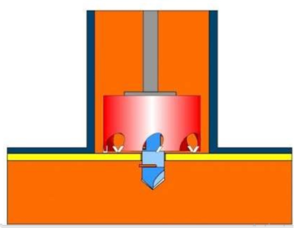
When the Pilot Drill is complete, the rotation is stopped. After this, the cutter shaft is advanced to allow U wires to drop. When the Cutter blades reach the top of the pipe, the rotation is once again started so that the cut can be completed.
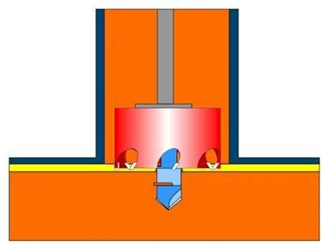
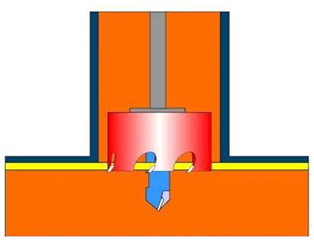
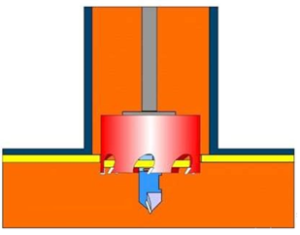
When the Cut is Completed, the machine is advanced to confirm that the tap is completed
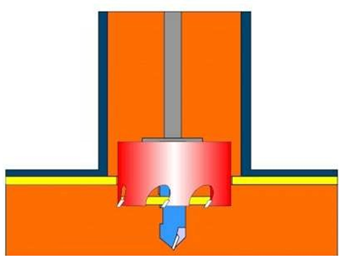
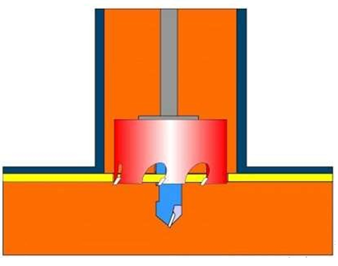

The Coupon and Cutter are withdrawn with the coupon or the cut-out is retained with U wires.
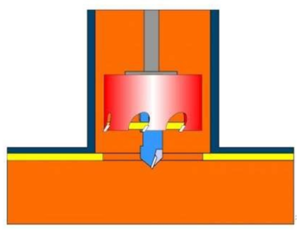
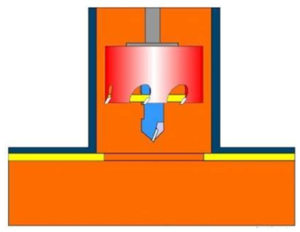
The Coupon Catcher Process in Action
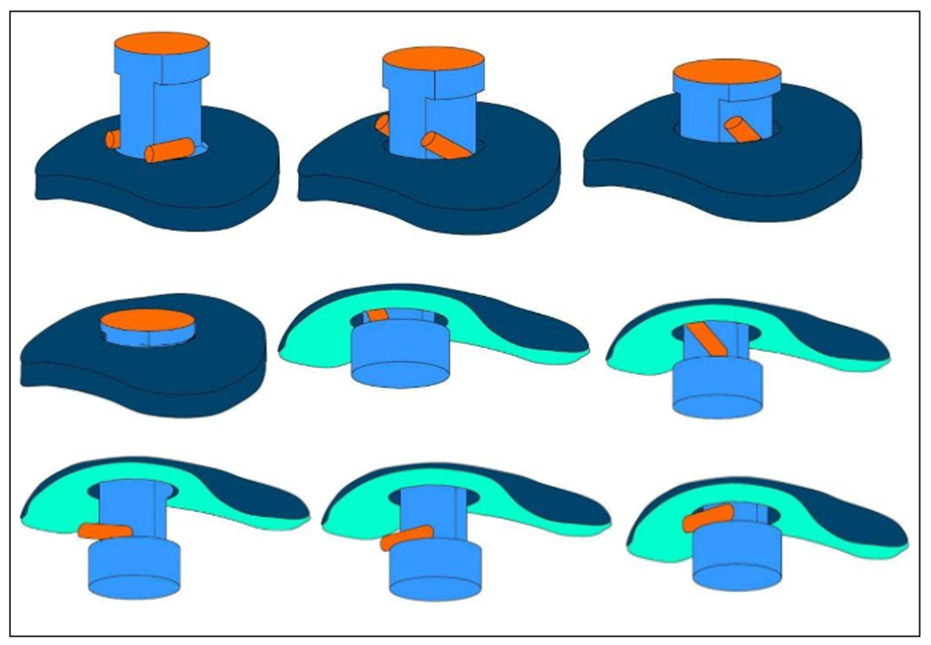
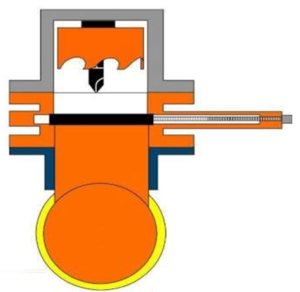
The Full Bore Gate Valve or Hot Tapping Valve is closed and the Hot Tapping Machine can now be removed
Additionally, Apart from Pipeline tapping unconventional Tapping requirements can arise for Tanks and Vessels. The Cutter for this purpose is different in geometry from the one used for live pipe tapping. The use of Split Tees and Saddles is not possible here as the diameter for these vessels prohibits that. The use of Weld-O-Lets and RF Pads is instead preferred.
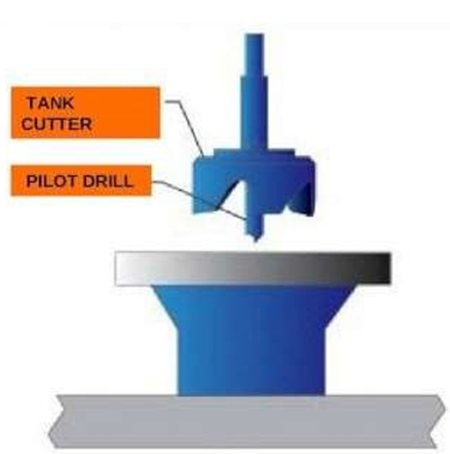
With This hot tapping procedure completed, it can be used for several processes. This includes pressure and temperature probes along with pressure evacuation/relief valves. Hot tapping also allows the use of line stopple machines and gas bags to be used. This is apart from the usual purpose of connecting new conduits & branch pipelines.
Factors to consider when performing hot tapping:
When planning a hot-tapping operation, there are several factors that must be considered.
- The integrity and safety of the existing pipeline must be ensured.
- The material, diameter, and pressure of the pipeline must be taken into account, and appropriate measures must be taken to ensure that the hot-tapping operation does not cause damage or compromise the integrity of the pipeline.
- The Mother pipeline and branch pipeline pressure are set ahead of the tapping. The orientation of the pipeline and tapping are taken into account along with the location of the pipe, whether it is underground and requires excavation or above ground and requires scaffolding for access.
- This adds to the costs that are associated with hot-tapping the scope of the work to be carried out and which contractor or subcontractor shall be responsible for the same.
- The appropriate type of Split Tee, Reinforcement pad, Weld -O – Let, and Valves are selected along with the type of hot tapping machine which differs as per the length of the cutter shaft and its travel length.
6. The valve must be able to withstand the pressure and temperature of the pipeline, and the tapping machine must be able to handle the material and size of the pipeline. The size and location of the tap must also be carefully considered, as it can affect the flow rate and pressure of the fluid or gas in the pipeline.
Precautions for the hot tapping operation:
Before the hot-tapping operation begins, the pipeline must be thoroughly cleaned and inspected to ensure that it is free of debris and defects. This is crucial to ensure that the tap does not cause any damage or blockages in the pipeline.
During the hot tapping operation, it is important to monitor the pressure and flow rate of the pipeline to ensure that the operation is proceeding smoothly. Any abnormalities or fluctuations in the pressure or flow rate should be immediately addressed to prevent any potential safety hazards.
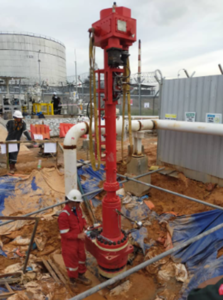
After the tap has been successfully installed, it is important to conduct post-installation testing to ensure that the connection is leak-free and meets the required pressure and flow specifications. This can involve various testing methods such as pressure testing, hydrostatic testing, and visual inspections along with Die penetrant and Ultrasound Testing of the pipe to check the integrity of the pipe.
Overall, hot tapping is a valuable technique for connecting whilst avoiding shutdowns and productivity losses. This a method that is gaining traction as economies of scale production in plants ensures that the production halts are very costly, something that hot tapping techniques avoid fully.
Leave a Reply