Flanges are an integral necessity in any industrial piping system owing to the role they play by linking pipes, valves, and other equipment. It is from such mechanical joints that fluid and gas transport systems are highly common in industries such as oil and gas power generation, petrochemicals, etc, which remain intact and effective. However, flanges frequently get damaged. Such a scenario may result in delays in operation and increased costs during maintenance and sometimes raise safety concerns.
In this blog, we’ll point out the common causes of flange damage and how such damage affects industrial operations. We’ll also introduce effective solutions from Tritorc, a leader in bolting, flange maintenance, and in-situ machining solutions, to address these challenges.
Common Causes of Flange Damage
1. Incorrect Bolting Practices
Bolts are also mandatory for tightening and then sustaining a flange connection. However, improper bolting techniques may be the improper application of torque or uneven tightening that causes uneven flange alignment or overstress. Then, eventually, deformation or leakage in a flange is caused. Similarly, the bolts may loosen because of minor torque too due to the contribution of vibrations that can also contribute to further damage of the flange.
2. Thermal Expansion and Contraction
In various high-temperature industrial processes such as oil refinery and power plants, flanges are constantly and periodically exposed to high temperature. If the temperature changes, expansions and contractions happen in materials and can be a cause of thermal fatigue. In reality, with repetitive cycles of heat, sometimes their stress can accumulate and result in warping of flanges or cracking at the joint, thus weakening the integrity of a flange.
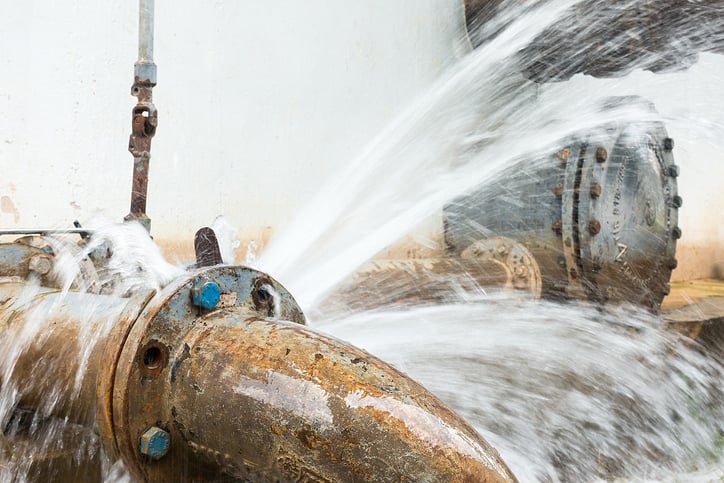
3. Corrosion
Among the primary causes of flange damage one such is corrosion, which can be due to exposure of the piping system to harsh chemicals, seawater, or moisture. Under such conditions, the metal material of the flange erodes, weakens, and tends to leak or even fail completely. This is particularly common with an offshore oil rig and petrochemical plants.
4. Mechanical Vibration
Mechanical vibrations is something that can never be fully prevented in heavy machinery and rotating equipment industries. If allowed to collect for quite a long period, these could loosen the bolts, misalign the flanges, or even crack material of the flange. It also aggravates this vibration, creating damaging feedback that affects not only the integrity of the flange but also the operational efficiency.
5. Improper Gasket Installation
Gaskets provide sealing between the two flanges, but wrong installation, using bad-quality gaskets, or wrong gasket materials lead to leaking. The confusion of misaligned gaskets, inadequate tightening of bolts, and damage on gasket surfaces lead to the decrease of pressure, which may cause leakage to the products, thus inefficiency in operations and hazards in safety.
6. Physical Damage During Installation or Maintenance
Flanges can physically get damaged during installation or while performing regular maintenance. This occurs if improper tools or excessive force is being applied. As a result, there will be scratches or dings on the flange or a misalignment that might prove complicated to correct. Apart from damaging physically, over time, the physical damage can weaken the flange such that under pressure, it might break.
Effects of Flange Damage on Industrial Operations
1. Increased Maintenance Costs
Flange damage often requires frequent inspections and repairs, which lead to increases in the cost of operations. In the absence of these regular checks, a tiny leakage or misalignment will shoot up into system failures, costly shutdowns, and hazardous leaks. The routine maintenance and flange replacement are costly when specialized labor is provided during the repair.
2. Unplanned Downtime
In case the joints leak or the flanges fail, the flanges might have to be repaired or changed. Down time becomes unplanned, and the production schedules are deeply affected which negatively impacts the timelines of projects and thereby gives rise to huge financial losses. A day of lost revenue in the oil-gas industry can be on a count of millions of dollars.
3. Safety Hazards
Damage to the flanges can pose severe threats of safety. Leakages, especially in high pressure or high temperature systems, can result in an accident in the form of fire or explosion. In any chemical and petrochemical industries, leakage of hazardous liquids can endanger the health and safety of an employee, causing legal liabilities and reputational damage.
4. Environmental Impact
Flange failure in industrial settings, therefore, can be large, even in areas which are sensitive to the environment. The examples include oil rigs and chemical plants which need massive expenditure on renewal during a flange failure. During flange failure, harmful chemicals, gases, or oil can leak uncontrolled into the environment and contaminate the water bodies, soil, and air. These releases can cause long-term damage to the environment resulting in adverse impacts on the marine life, local wildlife, and ecosystems.
Such incidents are also often linked to severe legal consequences, such as heavy fines and strict regulatory sanctions that are oftentimes attached in the violation of environmental protection laws. Beyond the financial losses, reputational damage to a company can be irreversible when public observation and loss of trust from stakeholders continue to increase over an event like an environmental catastrophe. For industries located in sensitive regions, flange integrity becomes not only an operational necessity but also a critical environmental responsibility.
Solving Common Flange Damage Issues with Tritorc’s Expert Solutions
- One of the main causes of flange damage is bad bolting practice and mechanical vibration, which leads to loose or misaligned flanges. This can be addressed by the hydraulic torque wrenches and bolt tensioners from Tritorc that apply precise and uniform force on all bolts; hence flanges remain tightly aligned and able to withstand mechanical vibration, avoiding any leakage, equipment failure, and other unplanned downtimes.
- Flanges are subject to thermal fatigue due to expansion and contraction. This can lead to warping or fatigue, but through the in-situ machining tools, like the flange facing machines provided by Tritorc, the status of flanges can be returned to as-new specifications even in extreme conditions. Regular maintenance and inspection through precision equipment reveal early signs of thermal fatigue before costly failures occur.
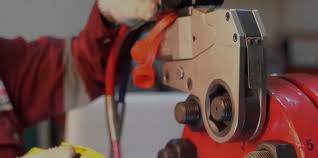
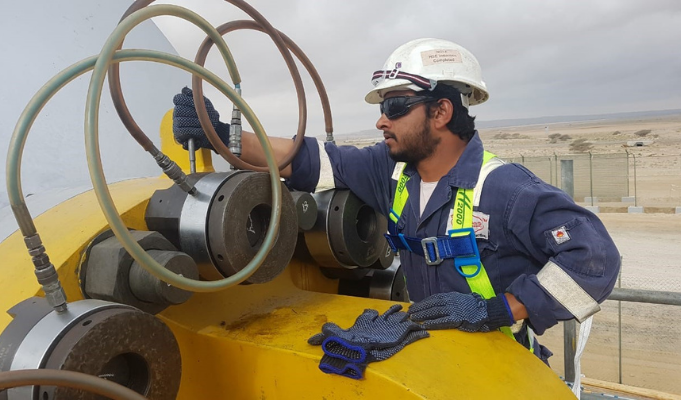
- Other common ills include corrosion and improper gasket installation. The trouble is addressed in Tritorc’s complete bolting and maintenance package by utilizing corrosion-resistant material and impact sockets to protect flanges from degradation. Further, Tritorc lets its operators choose and install the right gaskets through flange management systems which rely on accurate alignment and consistent bolt tension to present an extensively durable, leak-proof seal.
- Physical damage during installation or even maintenance can damage flanges and lead to additional failures. Tritorc provides cold cutting and in-situ machining solutions that facilitate accurate repair of flanges without creating further damages. These tools help create space for the integrity of flanges to be preserved so your operation remains uninterrupted and does not suffer from the after-effects of expensive downtime.
By combining advanced bolting, machining, and maintenance solutions, industries are able to minimize the risk of flange damage, reduce downtime, and help improve overall operational safety and efficiency.
Leave a Reply