Structural bolting joints present several difficulties, which can appear during the assembly process or in usage. There are many factors that affect how bolted joints behave in service and during assembly, which leads to these difficulties. The variables vary depending on the service and environmental factors, which have an impact on the bolts’ active energy.
How do Bolted Joints work ?
The commonly held notion is that the bolt in a bolted joint directly resists force. However, in reality, when you tighten the nut and bolt together, the bolt undergoes elastic stretching, generating force (known as clamp force) on the joint, similar to how a spring functions
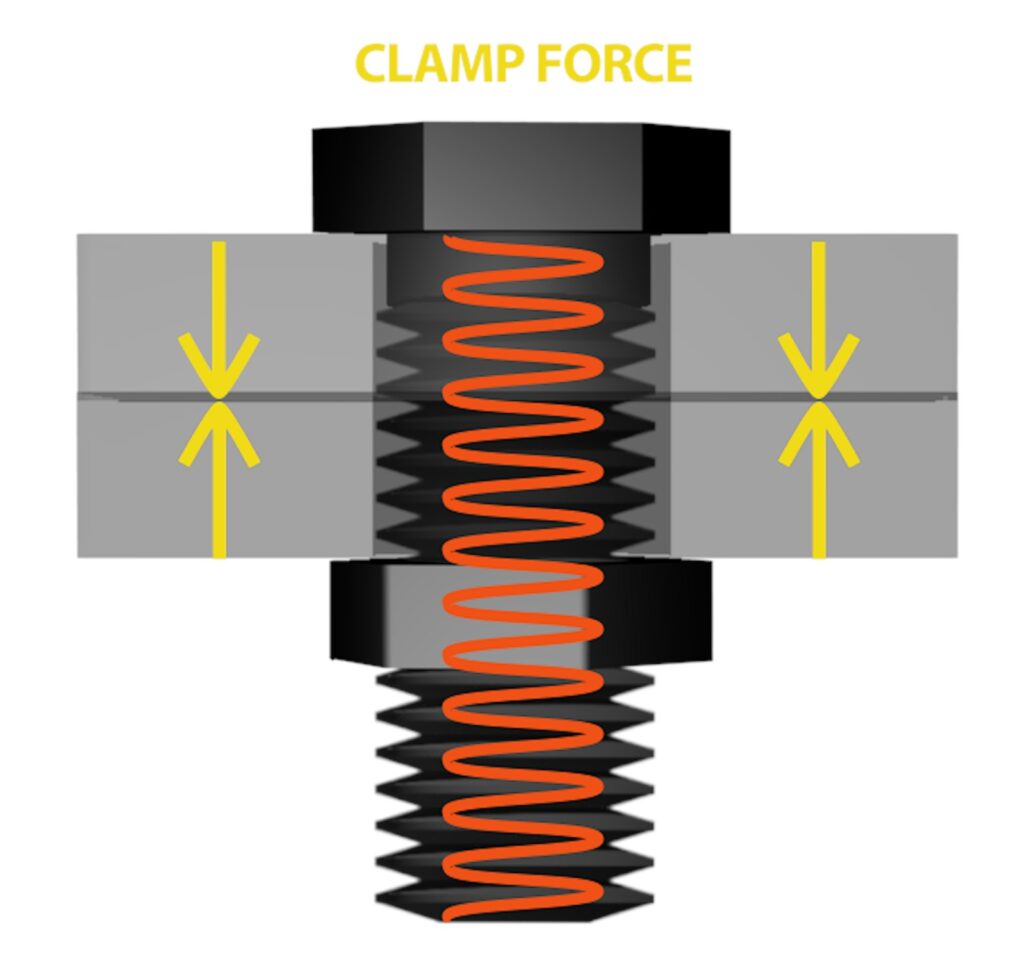
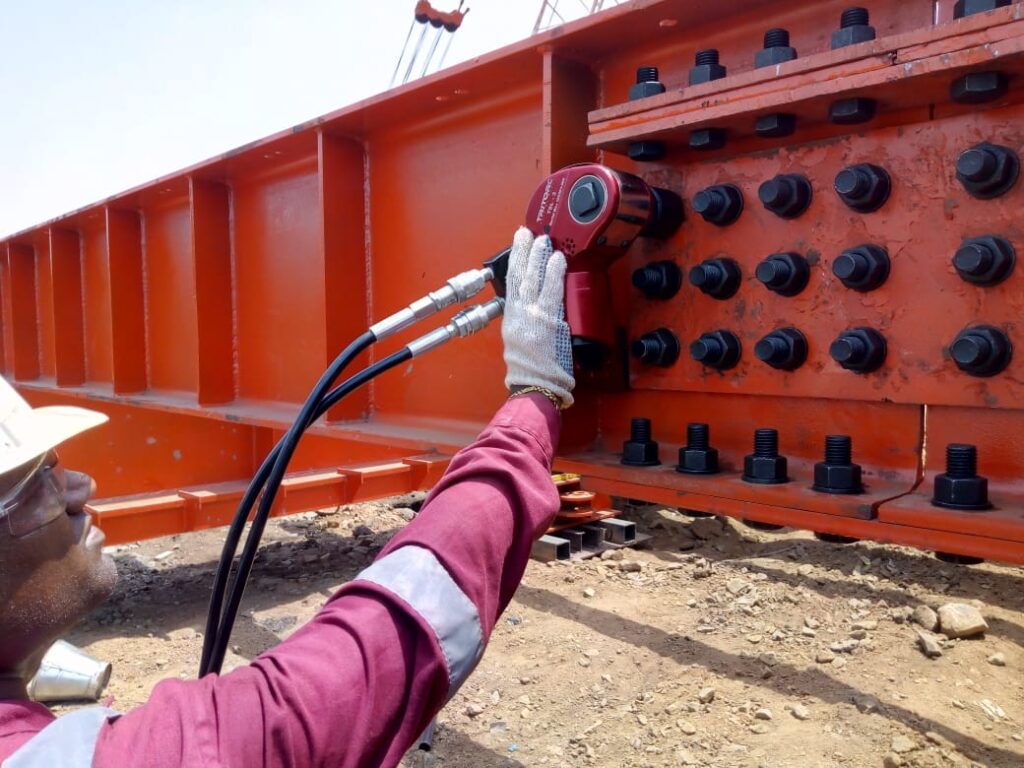
This force is created because of the friction between the two plates that are being joined together. When the bolt is correctly tightened, this force keeps the plates in place.
Insufficient tightening of the bolt can result in inadequate friction between the plates, causing the joint to loosen. Consequently, the force is directed onto the bolt, which can induce fatigue and eventually, breakage.
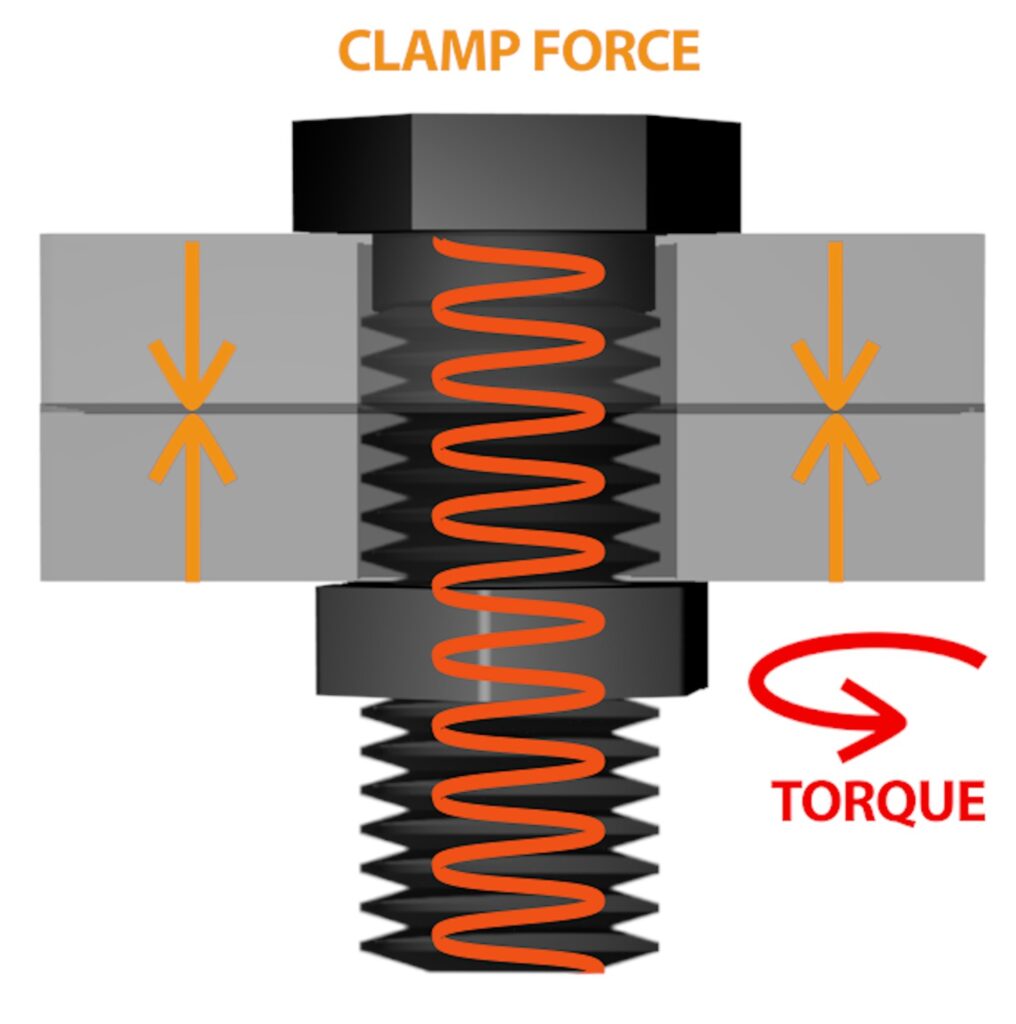
Customized Solution by Tritorc
TRITORC encountered a formidable challenge while providing bolting solutions to one of India’s largest bridges. The structure presented an intricate web of L-shaped bolts, nestled in hard-to-reach corners, posing a significant obstacle to conventional methods. Undeterred by the complexity, TRITORC rose to the occasion, deploying its innovative hydraulic torque wrenches in conjunction with specially crafted sockets.
This unique combination of cutting-edge tools, meticulously engineered by TRITORC, proved to be the key to unlocking access to the confined bolts. With unparalleled precision and efficiency, TRITORC’s solution not only facilitated seamless access but also averted the risk of bolt Protusion, ensuring the structural integrity of the bridge remained intact.
[1] Challenges faced during Assembly Process:
Making certain that the joint has an appropriate and ideal clamping force is the primary goal of the assembly procedure. The bolt and joint springs receive their initial energy from the clamping force. The longevity and behavior of such joints depend on the ideal amount of clamping force, so it must be made sure that it is neither below nor above that value.
“Typically, about 90% of the work on a bolt and nut is lost during the tightening, and only around 10% of the input work ends up as potential energy in the bolt; so only 10% ends up as bolt preload or as the clamping force between joint members.”
The remaining 90% is lost in following forms:
- Heat caused by friction among the nut and joint surface and among the male and female threads
- Energy lost to twisting and bending the bolt
- Energy lost to correcting the misalignment
- Energy lost to nut dilation [ whereby the energy is reduced owing to spreading the bottom of the nut]
Another reason for which a bolt may lose its energy is elastic interaction, whereby a bolt will relax owing to tightening of its neighboring bolt. This cause is even more challenging for the assembling process as it is more difficult to accurately predict the relaxation caused. The above mentioned assembly challenges are applicable to both tension and shear joints
[2] Stress variation in the flange joint components:
Ensuring a secure flange joint involves managing stress distribution within its components. Proper compression of the gasket across the flange face is crucial, which necessitates even tightening of bolts across the joint. Failure to maintain symmetry in tightening can lead to uneven compression, risking gasket damage. To achieve this, flanges should be gradually brought together, ensuring parallel alignment. This process typically begins with a correct bolt tightening sequence at a partial load, followed by multiple passes with increasing load each time.
The ASME PCC-1-2019 standard serves as the primary reference for bolting standards, providing various tightening sequences to achieve leak-free flange joints when followed accurately. While detailing every pattern for each flange size would require significant elaboration, here’s a brief overview of some examples.
[2.1] Star Legacy Pattern
This assembly procedure has been successfully applied throughout industry for all gasket styles and flange types. It is the standard “Best Practices” assembly procedure for bolted, flanged connections. In this pattern, bolts are tightened in a star-shaped or radial manner, starting from the bolts positioned at opposite ends of the flange and then progressively moving towards the center. This method helps distribute the load evenly across the gasket, ensuring uniform compression and minimizing the risk of leaks.
[2.2] Quadrant Pattern
A modified pattern that is simpler to follow than the Legacy pattern and does not require bolt numbers on the flange to be marked, as the next loose bolt in any given quadrant will always be the next bolt to tighten. This method has been successfully applied in limited applications across the full range of gaskets and joint configurations commonly found in the refining industry
[3] Proper Flange Alignment
Flanges are commonly used in piping systems to connect pipes, valves, and other components. Proper alignment of flanges is essential for a tight and leak-free connection. Flange misalignment can result in uneven load distribution, stress concentration, and increased risk of leakage. It is crucial to ensure that the flange faces are parallel and properly aligned during installation or maintenance activities.
Flange misalignment poses significant risks to industrial operations. When flanges are not correctly aligned, the gasket may not seat properly, leading to potential leaks. These leaks can result in environmental contamination, and product loss, and even pose safety hazards to workers and equipment. Additionally, flange misalignment can cause excessive stress on bolts, resulting in bolt failure and compromised structural integrity
From a safety aspect, by following the above information, what possibly could go wrong?
- Inadequate Training: If individuals conducting bolting operations are not adequately trained, they may not fully understand the procedures and safety precautions, leading to errors and accidents.
- Tool Calibration Errors: Torque wrenches and tensioning devices must be accurately calibrated. If calibration is not performed correctly or on schedule, bolts may not be tightened to the required specifications, risking joint failure.
- Poor Maintenance: Neglecting the maintenance of bolting tools and equipment can lead to malfunctions or inaccuracies, jeopardizing the quality and safety of bolted joints.
- Misapplication of Torque/Tension: Using the wrong method (torque or tension) for a specific application can result in under-tightened or over-tightened bolts, which can compromise joint integrity.
- Lack of Quality Control: Inadequate documentation, record-keeping, and quality control measures may lead to uncertainty about the condition of bolted joints and hinder the ability to identify potential issues.
- Improper Flange Alignment: Misaligned flanges can cause excessive stress on bolts, leading to joint failure. Proper alignment is crucial to prevent this issue.
- Inadequate Lockout/Tagout: If lockout/tagout procedures are not followed rigorously, equipment may inadvertently start during bolting operations, posing a severe safety risk.
- Emergency Response: Inadequate preparation for emergency situations, such as leaks or equipment failures during bolting, can result in delayed or ineffective responses.
- Improper Torque/Tension Control: Failing to monitor and control torque or tension levels during the tightening process may result in bolts being under- or overtightened, compromising joint integrity
To mitigate these potential safety risks, it’s crucial to:
- Ensure that all personnel involved in bolting operations receive proper training and certification.
- Implement a robust quality control program, including thorough documentation and record-keeping.
- Regularly inspect, calibrate, and maintain bolting tools and equipment.
- Follow industry-specific safety regulations and standards.
- Promote a safety culture within the organization, emphasizing the importance of safety in bolting activities.
- Encourage open communication and reporting of safety concerns or incidents.
Leave a Reply