Project Overview
In February 2024, ADNOC approved a critical retubing project at the Samsung Abu Dhabi Oil and Gas Refinery Plant.
The primary objective was to address significant operational issues, including pressure drops and leaks in the heat exchangers, which compromised the plant’s efficiency and safety. The project commenced on February 26, 2024, with an anticipated completion time of one month.
Why is Retubing Required?
Plant shutdowns, also known as “turnarounds,” are critical periods for oil and gas refineries. These shutdowns can significantly influence the financial outcomes and future commitments of the plant, either positively or negatively.
Among the essential equipment in these refineries is the heat exchanger, which plays a vital role in various processes and heat transfers. The performance of heat exchangers also impacts the duration of plant turnarounds. After a turnaround, if a heat exchanger fails shortly after normal operations resume, it can lead to substantial financial losses due to reduced downtime or decreased production, despite the contractor’s warranty.
During turnarounds, heat exchangers may undergo various repairs, including partial or full retubing through different methods or simple plugging. Repairing heat exchangers during these periods helps minimize downtime losses and ensures the equipment’s integrity for the smooth operation of the plant.
Project Specifications
- Plant Type: Oil and Gas Refinery
- Equipment: Heat Exchangers
- Tube Specifications:
- Outer Diameter (OD): 15.88 mm
- Thickness: 0.7 mm
- Material: Titanium (for corrosion resistance and strength)
- Tube to Tube Sheet Expansion: Expanded type
- Equipment Position: Horizontal, elevated at 7-8 meters
- Tube Sheet Condition: Highly rusted and corroded
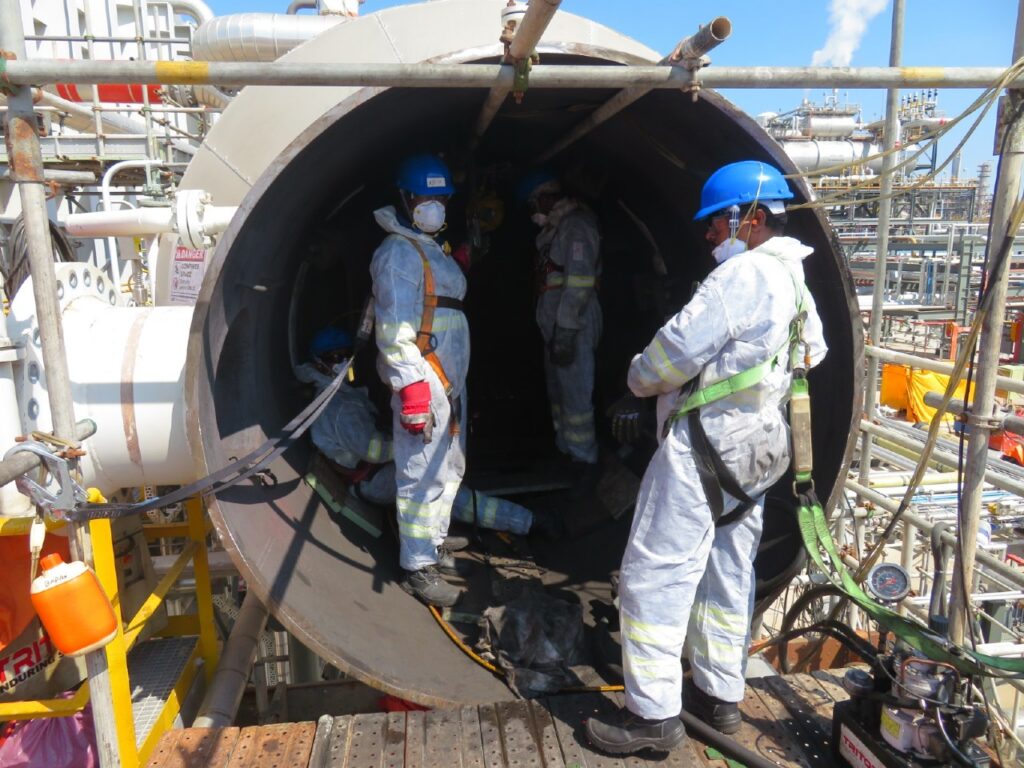
Challenges and Solutions
1. Confined Space Operations:
- Retubing required technicians to operate in a confined space of 2.5 meters and at an elevation of 7-8 meters, entering through a manhole with limited oxygen availability.
- Solution:
- Technicians received specialized training for confined space operations, including safety protocols for low-oxygen environments.
- Technicians had specialized permits to work in confined spaces to carry out the retubing operation.
- A scaffolding platform was built so that the technicians can carry out the job at a specified height.
- Appropriate safety equipment, including oxygen supply systems, was utilized to ensure the safety of the workforce.
2. Material Handling:
- Titanium tubes are critical and sensitive materials requiring careful handling to avoid damage.
- Solution:
- Use of specialized tools and equipment procured by Tritroc to handle and install the titanium tubes without compromising their integrity.
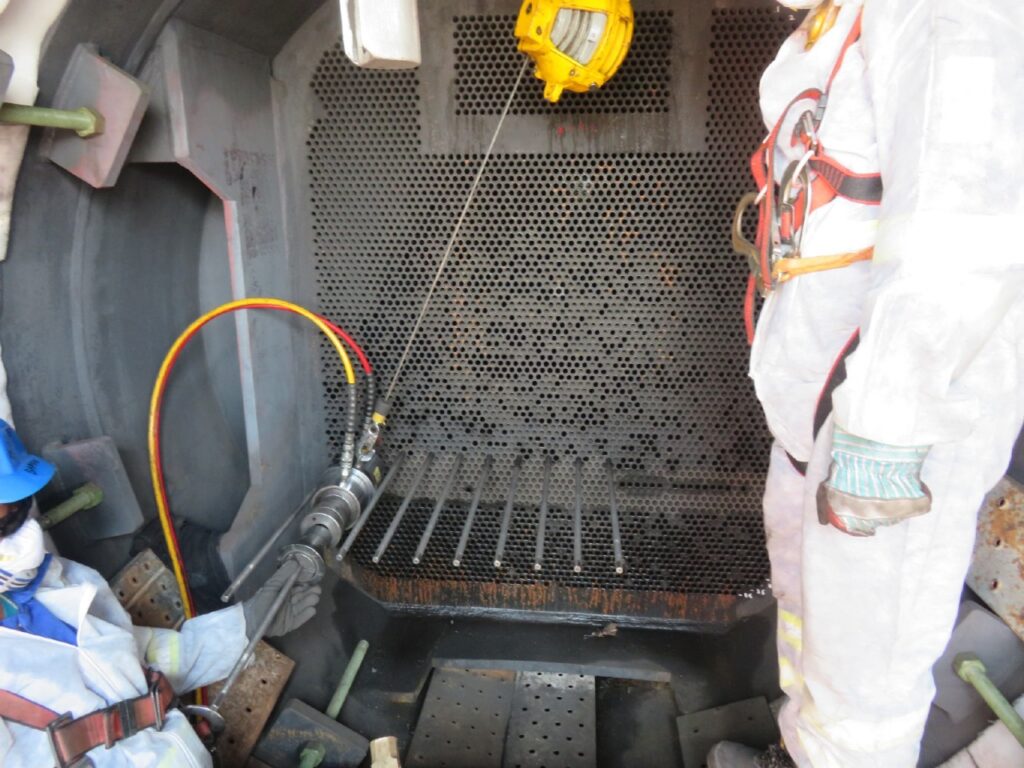
With the assistance of impact wrenches paired with sockets, the insertion of mandrels into the tubes was facilitated. Tritorc’s Hydraulic Tube Pulling Gun, powered by the STPP 300 Electric Pump, efficiently extracted the tubes for replacement. To optimize the functionality of the pulling gun, a spring-loaded balancer was employed to suspend it, ensuring smoother operations.
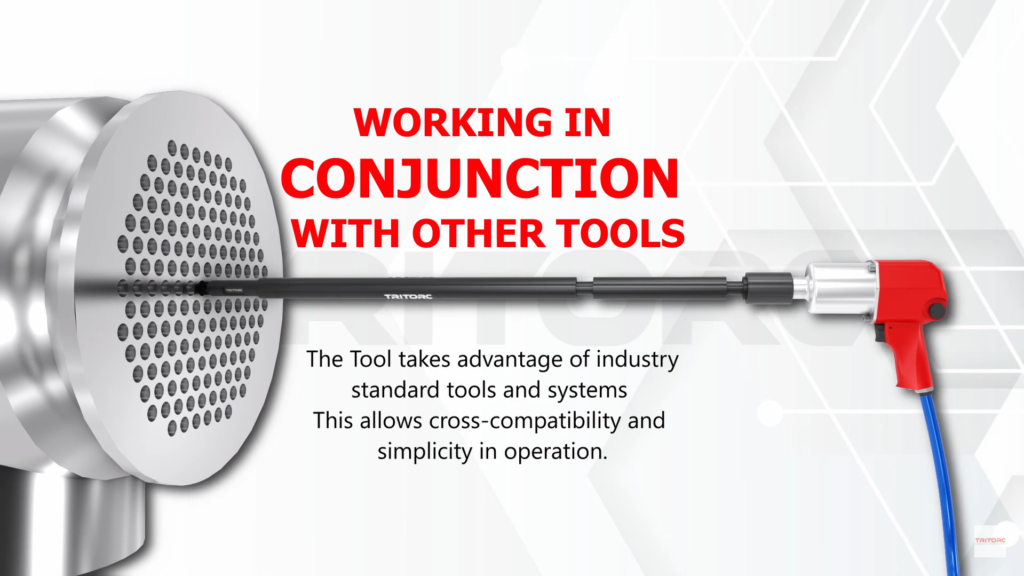
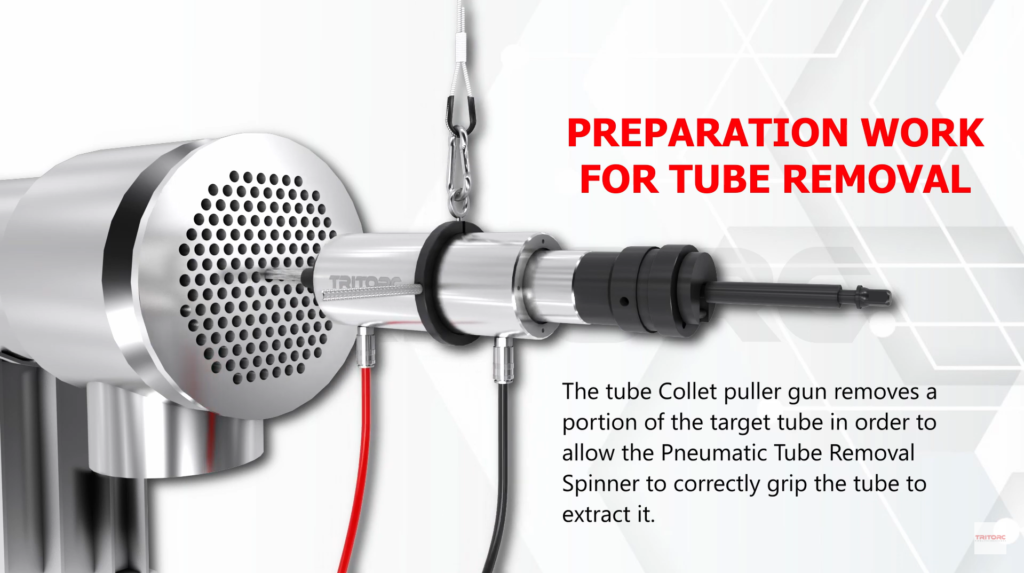
3. Operational Efficiency:
- The retubing needed to be completed within a tight schedule to minimize downtime.
- Solution:
- Tritorc efficiently cleaned 40,000 tubes within 7-8 days, preparing the heat exchangers for retubing.
- A workforce of 14 technicians, including 2 supervisors and 12 technicians, ensured round-the-clock operations to adhere to the project timeline.
4. Safety and Training:
- Ensuring the safety and certification of technicians working in hazardous environments.
- Solution:
- Comprehensive training programs were conducted, covering various operational environments, such as H2S exposure, working at heights, and confined spaces.
- Medical examinations and certifications were mandatory, provided by ADNOC, to clear technicians for the retubing operation.
Project Execution
[1] Inspection and Documentation:
- Initial inspections and documentation were completed to assess the extent of corrosion and plan the retubing process.
[2] Retubing Operations:
- Technicians performed retubing from the confined space, meticulously expanding the new titanium tubes into the rusted and corroded tube sheets.
- The operation was executed under stringent safety protocols, with continuous monitoring of oxygen levels and adherence to confined space safety regulations.
[3] Project Completion:
- The project was completed within the scheduled timeframe of one month, with all 40,000 tubes successfully replaced and operational.
[4] Adherence to Standards:
- A standardized procedure was incorporated to satisfy all the standard codes like ASME, TEMA, SAES, SES, and NBIC.
Outcome
The retubing project at the Samsung Abu Dhabi Oil and Gas Refinery Plant was a critical maintenance operation that successfully addressed the issues of pressure drops and leaks in the heat exchangers.
Through meticulous planning, specialized training, and the use of appropriate tools, the project was completed safely and efficiently. The plant resumed operations with enhanced efficiency and safety, meeting ADNOC’s high standards of operational excellence.
This case study exemplifies the importance of thorough preparation, a skilled workforce, and adherence to safety protocols in executing complex maintenance projects in the oil and gas industry.
Leave a Reply