A hydraulic powerpack powers hydraulic torque wrenches, while a hydraulic tensioner pump drives bolt tensioners. These pumps serve as critical energy conversion devices by transforming mechanical energy into fluid pressure energy to operate high-force industrial tools.
These powerpacks are powered by an electric motor or an internal combustion engine. The pump draws hydraulic fluid from a reservoir, pressurizes it, and delivers it to the actuator to ensure controlled force in bolting applications.
These pumps are the power source for hydraulic torque wrenches and bolt tensioners. They are widely used in high-load industries such as oil and gas, power generation, EPCs, and heavy machinery maintenance. They provide the necessary force for accurate, repeatable, and safe bolt tightening, preventing structural failures and ensuring operational reliability.
How Does a Hydraulic Power Pack Work?
A hydraulic power pack operates by converting mechanical movement into hydraulic pressure. When the pump starts, the cam rotates, causing the plunger to rise and compress the hydraulic fluid, forcing it out through a one-way valve. As the cam rotates downward, a vacuum effect pulls in fresh hydraulic fluid from the reservoir. This continuous cycle of suction and discharge ensures a steady flow of pressurized fluid to the connected tool.
The effectiveness of a hydraulic pump depends on:
- Flow rate (L/min): This determines speed and efficiency.
- Maximum pressure (bar/psi): To define force capacity for different applications.
- Pump type varies based on power source, workload, and operational requirements.
Types of Hydraulic Pumps and Their Applications
Hydraulic pumps are classified based on their application and power source:
1. Application-Based Classification
- Hydraulic Torque Wrench Pumps: Typically operate at 70 MPa (10,000 psi) for controlled torque applications.
- Hydraulic Tensioner Pumps: Designed for bolt tensioning, reaching pressures up to 150 MPa (21,750 psi) for high-load precision applications.
2. Power Source-Based Classification
- Electric Hydraulic Pumps: Driven by an electric motor (110V/230V single-phase or 380V/440V three-phase), offering accurate torque application. High-powered, brushless motors extend lifespan and reduce maintenance.
- Pneumatic Hydraulic Pumps: Powered by compressed air, ideal for hazardous or explosion-prone environments due to their spark-free operation. They operate at 6–10 bar (90–145 psi) and provide consistent power.
- Manual Hydraulic Pumps: Hand-operated, made from aluminum-titanium alloy, offering lightweight, corrosion-resistant performance for portable applications.
How to Use a Hydraulic Powerpack for Bolting Applications
Using a hydraulic pump efficiently requires careful evaluation and setup. Here’s a step-by-step guide:
- Assess Bolting Requirements: Determine bolt diameter, nut size, bolt grade, washer thickness, and preload requirements to select the correct hydraulic pump and tool.
- Connect the System: Use high-pressure hoses to link the hydraulic pump to the torque wrench or tensioner securely.
- Set up the Tool: Place the hydraulic torque wrench or tensioner onto the bolt or nut.
- Activate the Pump: Start the pump to deliver high-pressure hydraulic fluid, engaging the piston to apply torque or tension.
- Monitor Pressure Levels: Ensure the working pressure stays within the recommended range for optimal performance.
- Complete the Tightening Cycle: Once the desired bolt load is achieved, release pressure, retract the piston, and verify the bolt’s final position.
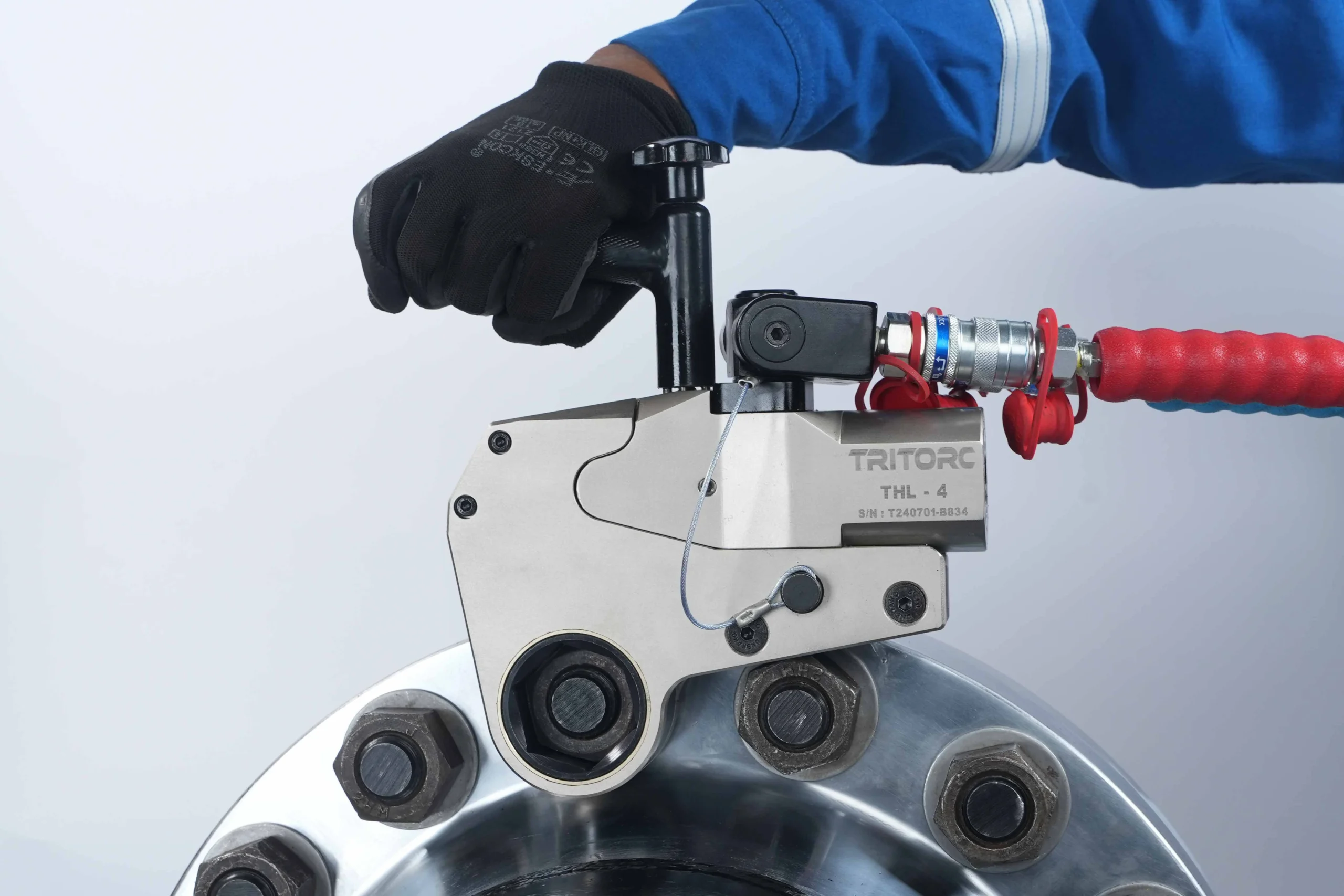
By selecting the right hydraulic pump and following proper operational steps, industries can achieve precise bolt tightening, enhanced safety, and reduced downtime in critical applications.
Operator Coordination in Torquing Activities
In hydraulic torque operations, proper coordination between operators is essential for safe and efficient execution. Typically, two operators are involved: a pump operator who controls the hydraulic pump, regulating pressure and flow to the torque wrench, and a torque applicator who manages the application of torque, ensuring correct tool placement and work-load distribution.
Why Coordination Matters:
- The pump operator must adjust the pressure precisely based on the torque applicator’s signal to prevent overloading or under-torquing the bolt.
- Miscommunication can result in sudden pressure spikes, leading to tool failure, joint misalignment, or personal injury.
- Synchronization ensures that torque is applied evenly and consistently, maintaining bolted joint integrity.
Steps to avoid mishaps:
- Conduct a pre-torquing checklist review to ensure the tool is set up correctly.
- Use incremental torquing rather than applying full force in one go, minimizing the risk of bolt damage.
Not only in touring applications, but coordination is crucial in tasks working with powerpacks. Proper teamwork between operators enhances safety, improves bolting accuracy, and extends the lifespan of hydraulic tools, making it a vital aspect of professional torque applications.
Leave a Reply