Tube expansion is a vital heat exchanger and boiler production process, which gives a secure and leak-free joint between the tube sheet and the tube. To establish a strong tube-to-tube sheet bond, the expansion process requires mechanically increasing the tube’s diameter inside the tube sheet hole.
Perfect tube expansion calculations are essential to prevent under-expansion, which could lead to leaks, or over-expansion, which could weaken the tube or damage the tube sheet.
The calculation takes into account parameters like tube outer diameter (OD), tube wall thickness, tube hole diameter, and the percentage of expansion needed.
Role of Tube Expansion
The general concept of tube expansion is to plastically deform the tube wall against the tube sheet hole to create a pressure-tight seal. A tube expander rolls the tube within the hole to achieve this.
The amount of expansion is measured by the percentage increase in the tube’s outer diameter over its original dimension. The process of expansion should make sure that the tube does not thin too much, losing mechanical strength, or overpass the elastic limit of the tube sheet, which would result in damage.
Formula for Tube Expansion
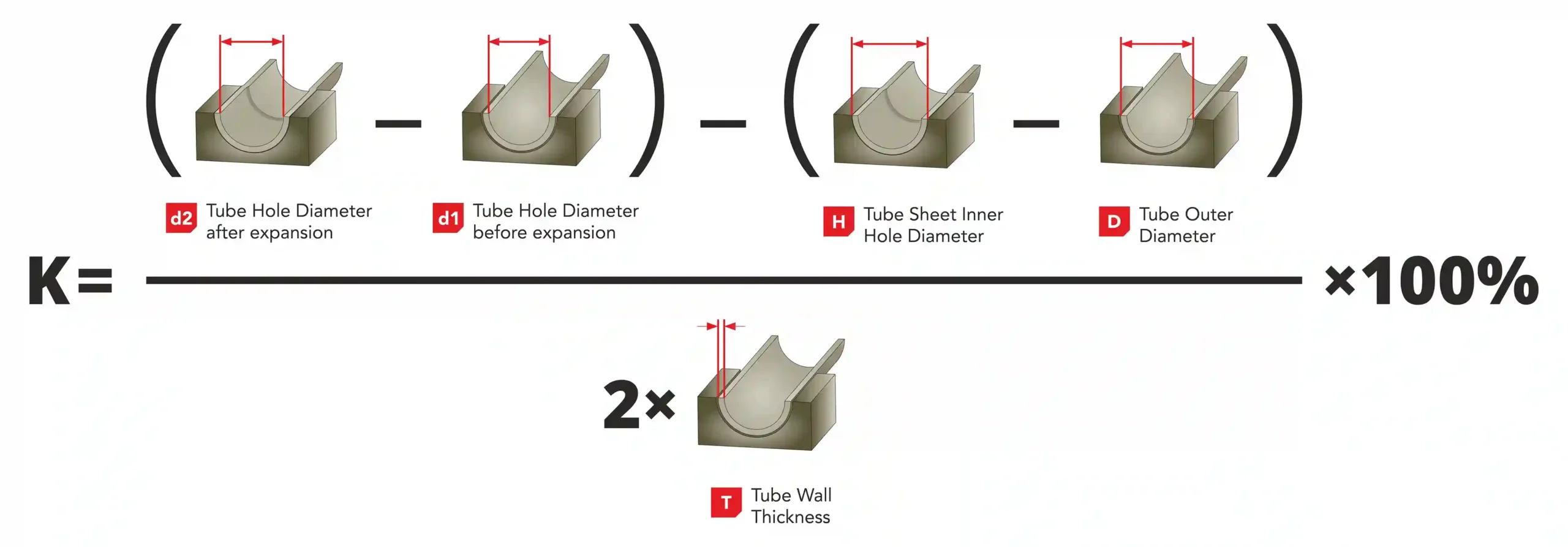
Where:
- K = Percentage of tube expansion
- d2 = Tube hole diameter after expansion (mm or inches)
- d1 = Tube outer diameter before expansion (mm or inches)
- H = Tube sheet inner hole diameter (mm or inches)
- D = Tube outer diameter (mm or inches)
- T = Tube wall thickness (mm or inches)
- d3 = Tube inner diameter (mm or inches)
- C = Clearance
Generally, the percentage of expansion varies between 3% and 9%, depending on tube material, tube sheet material, and application. Overexpansion will decrease the residual wall thickness and weaken mechanical strength, while underexpansion will cause leakage.
Formula for Clearance
Clearance is the gap that allows room for expansion of the tube during the expansion or rolling process. When the tube is mechanically expanded using a tube expander, it presses outward and makes a tight, leak-proof fit against the tube sheet hole wall.
Proper clearance ensures the correct amount of wall thinning and secure mechanical grip, which is an important factor for heat transfer and leak-free operation.
Formula for Clearance
C = H − D
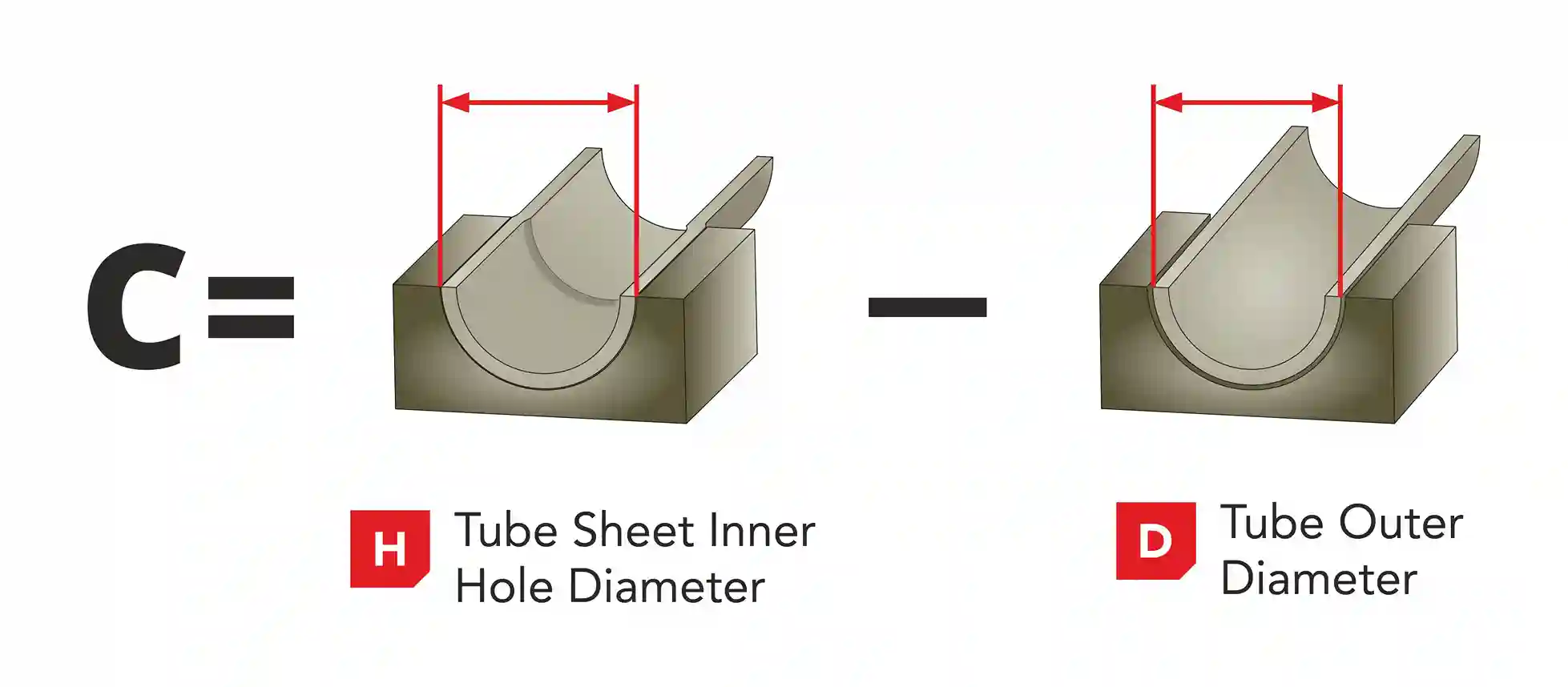
- H = Tube sheet inner hole diameter (mm or inches)
- D = Tube outer diameter (mm or inches)
- C = Clearance
Formula for After Expansion ID
The after-expansion inner diameter helps us to verify how much the tube has thinned during the expansion process. It ensures the expansion is within safe limits and that the tube still meets flow and strength requirements.
After Expansion ID
d2 = ((T X 2) X K) + d3) + C

Where:
- K = Percentage of tube expansion
- d2 = Tube hole diameter after expansion (mm or inches)
- T = Tube wall thickness (mm or inches)
- d3 = Tube inner diameter (mm or inches)
- C = Clearance
Formula for Inner Diameter of the Tube
Even after understanding all the formulas and parameters involved in tube expansion, such as wall thickness, expansion percentage, and clearance through the above formulas, there may be instances where you need to reverse-engineer the inner diameter of the tube. Either you may be double-checking expansion allowances or preparing for retubing; having the inner diameter is crucial. If that’s the case, here’s a simple way to calculate:
Inner Diameter of the Tube
d3 = D – 2T
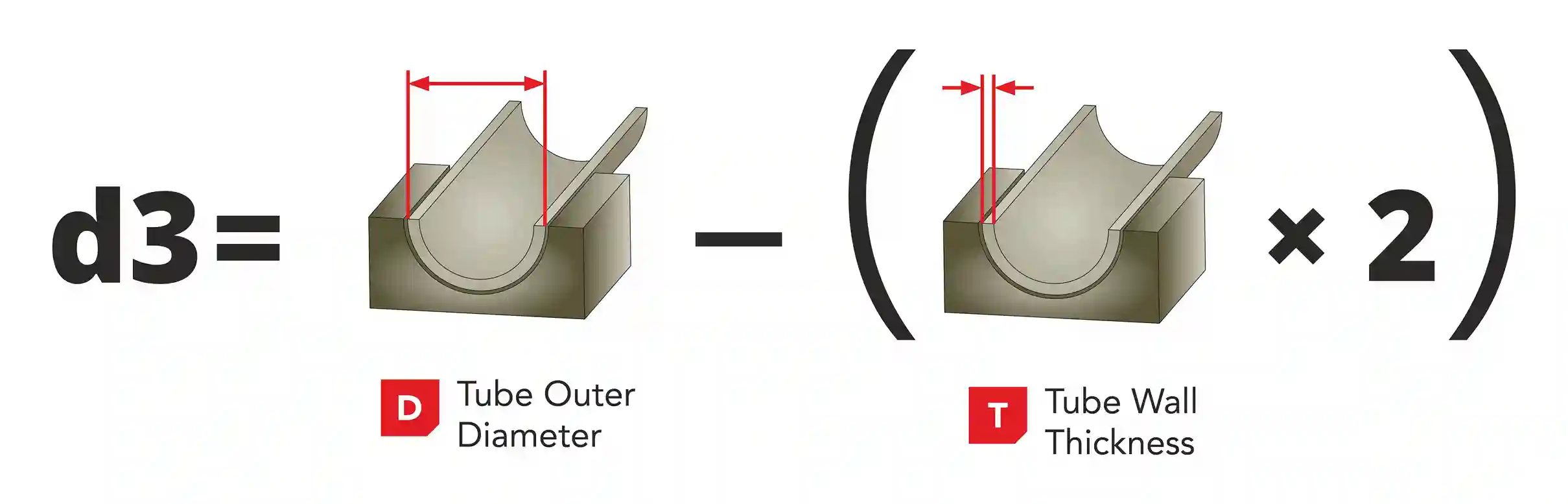
Where:
- d3 = Tube inner diameter (mm or inches)
- D = Tube outer diameter (mm or inches)
- T = Tube wall thickness (mm or inches)
Factors Affecting Tube Expansion
Tube Material
The tube material is significant in the determination of the force needed for expansion. Less expansion force is needed for softer materials such as copper or aluminum, while harder materials such as stainless steel, titanium, or Inconel need much more force to expand appropriately.
Tube Sheet Material
It is necessary to ensure the tube and tube sheet material compatibility for attaining good bonding. In the case of softer tube sheets than the tube, there will be an increased risk for deformation, while harder tube sheets need more expansion forces.
Wall Thickness
The wall thickness of the remaining tube after expansion must be adequate to carry operational loads without failure. Excessive thinning through over-expansion reduces the structural integrity of the tube, while under-expansion can fail to create a good seal.
Tube Hole Tolerance
Diameter variations in tube holes within the tube sheet can affect the ultimate expansion percentage. A larger hole size requires greater expansion, whereas a tighter hole fit requires reduced rolling.
Expansion Method
Varying expansion parameters, including the type of expansion, have impacts on the final expanded diameter and joint integrity. Mechanical rolling is the preferred method based on precision and repeatability.
Lubrication and Tooling
Adequate lubrication minimizes friction and protects both the tube and expander tooling from damage. The proper design of the tube expander and roller sizes provides even expansion and avoids localized thinning or stress concentrations.
Residual Stress and Work Hardening
Expansion puts residual stress on the tube and tube sheet that influences long-term performance. Too much expansion can result in excess hardening, causing them to become brittle and more prone to corrosion and cracking.
Leave a Reply