In a landmark project showcasing technical prowess and industry-leading capabilities, Tritorc has successfully completed a crucial heat exchanger retubing and maintenance operation in Uzbekistan’s oil and gas sector. This project, focusing on oxygen preheaters, highlights Tritorc’s position as a complete solution provider for heat transfer equipment maintenance in challenging environments.
Tritorc’s engineers demonstrated their versatility by successfully removing and replacing 41 tubes from one heat exchanger and 161 from the other, showcasing their ability to handle projects of varying scales with equal proficiency.
Project Overview and Significance
The scope of work encompassed the meticulous retubing of oxygen preheaters, vital components in the oil and gas industry that enhance process efficiency by preheating oxygen before it enters various operations. Oxygen preheaters play a crucial role in the industry by increasing the temperature of oxygen, typically using steam or hot gases as the heating medium, while oxygen flows through the tubes.
This preheating process improves overall system efficiency and safety in “Gas to Liquid applications.” The oxygen preheater operates in a demanding environment, making precision retubing a non-negotiable factor,” explained Piyush Panchal, Tritorc’s subject matter expert in Heat transfer business division. “Given the medium was oxygen, we ensured a full-proof solution with Tube replacement, enhancing reliability.”
Adherence to Global Standards
Adhering strictly to TEMA & ASME standards for heat exchanger design, standards for quality control, Tritorc’s project engineers and site supervisors ensured that every aspect of the maintenance process met the highest industry benchmarks. The company’s commitment to quality was evident in their comprehensive documentation process, which included detailed Hydrotest reports, Daily progress updates, Repair and inspection plans, Safety procedures, Method statements, Work completion reports, and Quality control work cross-checked against meticulously prepared method statements.
Technical Approach and Execution
Tritorc’s technical approach was both innovative and precise. Utilizing state-of-the-art hydraulic power packs, the team executed a multi-step process that included:
- Plug removal using annular cutters.
- Weld removal and ID-mounted weld removal & bevelling for smooth tube sheet preparation
- Tube pulling using hydraulic power tools
- Cleaning of tubes with industrial brushes and degreaser
- Tube insertion and welding followed by controlled expansion
The project involved the removal of 41 and 161 tubes from two heat exchangers, respectively. This partial retubing job focused on removing tube plugs and expanding surrounding tubes.
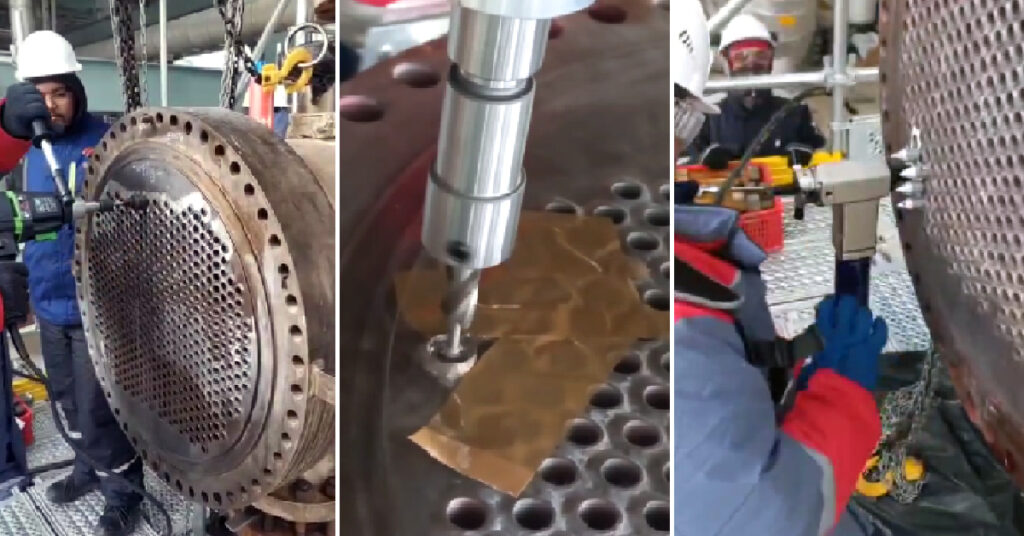
“Each retubing project is unique,” noted Panchal. “Tensile strength, tube material, and environmental factors dictate the approach. Here, we followed a controlled sequence—plug and weld removal, precision ID bevelling, hydraulic tube pulling, and systematic expansion.”
Detailed Work Methodology
Tritorc deployed a structured approach for safe and efficient execution:
Tube Plug Removal & Weld Removal:
- 90 plugs were removed using hot work, annular cutting, and ID-mounted weld removal tools.
- External tube sheet welds were removed using angle grinders to allow full access to tube removal.
- Tube guides were placed to prevent debris from entering existing tubes and guide the tubes through baffles.
Tube Removal Techniques:
- If tubes were stuck, drilling was performed to reduce wall thickness before pulling.
- Drifting & collapsing were used as backup methods.
- Hydraulic gun with power pack was employed for direct tube removal.
Tube Cleaning & Preparation:
- Holes were cleaned using tube sheet hole brushes & degreasers before new tube insertion.
- Tube end facers were used for tube projection adjustments.
- Visual inspection of tube sheets ensured no contamination or damage
Tube Insertion & Expansion:
- New wrapped tubes supplied by the client were inserted with tube guides.
- Expansion was executed using MPG-2N German Electrical Expansion Drive with a 1600-watt torque controller.
- A step-by-step light expansion sequence ensured proper fitment.
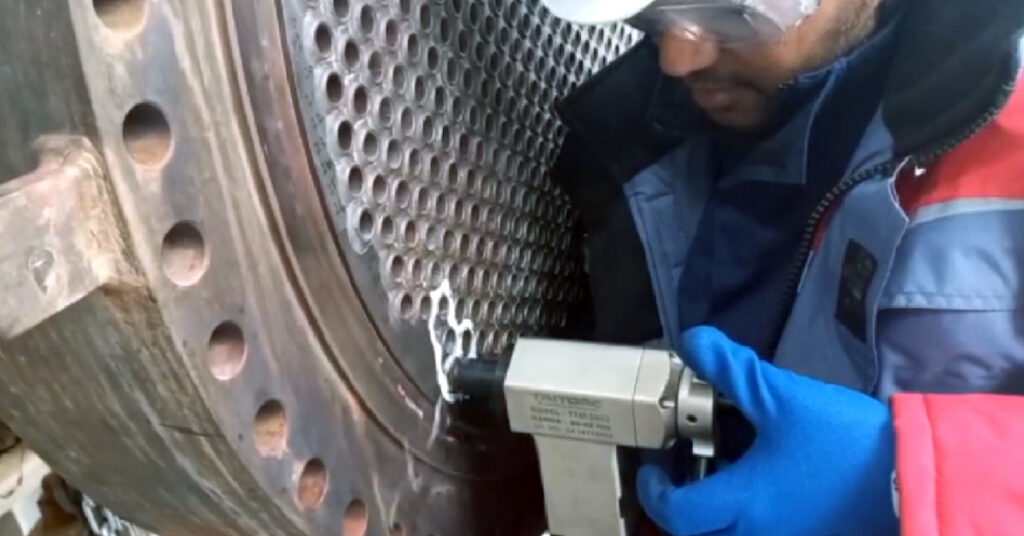
Final Testing & Quality Control:
- Hydrotesting was conducted to verify tube integrity.
- Compressed air blowing was used for final tube cleaning.
- NDT testing ensured no expansion cracks.
“Our QC measures were rigorous,” stated Panchal. “We provided hydrotest reports, daily progress tracking, inspection plans, radiography reports for welder qualification, and work completion documentation. Every detail was meticulously checked against our method statement.”
Challenges and Adaptability
Despite Uzbekistan’s challenging cold climate, the team maintained efficiency and precision throughout the maintenance process. Work area sealing and controlled personnel entry were implemented to maintain operational integrity. The project was completed in an impressive 15-20 days per exchanger, showcasing Tritorc’s efficiency and expertise.
Comprehensive Industrial Solutions
With expertise in Pipeline Process Services (PPS), flange management, and heat transfer equipment, Tritorc reaffirmed its position as a comprehensive service provider for industrial maintenance and engineering projects. Their experience extends to various applications in the thermal power sector, including high-pressure lines, steam presses, and turbines.
“This wasn’t just a maintenance job—it was a precision-driven solution,” Panchal emphasized. “At Tritorc, we engineer reliability that stands the test of time.”
As the oil and gas industry continues to evolve, with an increasing focus on efficiency and reliability, Tritorc’s demonstrated expertise in heat exchanger maintenance positions them at the forefront of industrial service providers. Their ability to combine cutting-edge technology with strict adherence to international standards ensures that critical heat transfer assets remain operational and efficient, even in the most demanding environments.
Conclusion
“This project represents one of our most significant and successful endeavors in the Central Asian market,” said a senior executive at Tritorc. “Our long-term strategy of investing in local infrastructure and talent has paid off, allowing us to respond swiftly to client demands and establish ourselves as a trusted partner for major operators in the region.”
Leave a Reply