- Corrective maintenance : When a fault is detected in equipment, corrective maintenance is called into action. Its primary goal is to restore the equipment’s functionality and performance to the required level. Corrective maintenance can be planned or unplanned, depending on whether a maintenance plan existed prior to the failure.
- Preventive maintenance : Preventive maintenance aims to reduce the likelihood of equipment failure by preventing potential problems from occurring. Maintenance teams use historical data and failures to create well-structured maintenance programmers. This allows them to identify potential failure points and take preventive measures to reduce risk.
- Risk-Based Maintenance : Risk-based maintenance is intended to address risk-sensitive systems and machinery. Its primary goal is to efficiently allocate resources to reduce or repair risks in order to ensure the safety of employees, employers, and company assets.
- Condition based Maintenance : Condition-based maintenance is a type of predictive maintenance that relies on sensor data, such as vibration monitoring systems, to assess the condition of equipment while it is in operation. Maintenance actions are only triggered when the predictive maintenance dataset indicates a decline in equipment performance.
- Predetermined Maintenance: Predetermined maintenance is the least popular predictive maintenance method, as it relies solely on the maintenance programs provided by equipment manufacturers rather than monitoring the actual equipment condition. These programs are based on the manufacturers’ knowledge of failure mechanisms and past MTTF (mean time to failure) data.
Industries where Predictive Maintenance is required
- Manufacturing
- Energy
- Transportation
- Oil and Gas
- Healthcare
Why is Predictive Maintenance so Important in the Oil and Gas Industry
An average oil and gas company experiences at least 27 days of unplanned downtime each year, costing $38 million. Even if the downtime lasts only 3.65 days, the resulting losses could be as much as $5 million. This is why PREDICTIVE MAINTENANCE is so important. Predictive maintenance technologies utilize artificial intelligence, machine learning, and advanced analytics to identify issues and notify technicians, reducing equipment failure and safety risks.
“According to a McKinsey report, an offshore oil and gas company used a predictive maintenance solution to reduce downtime by 20% and increase production by over 500,000 barrels per year.“
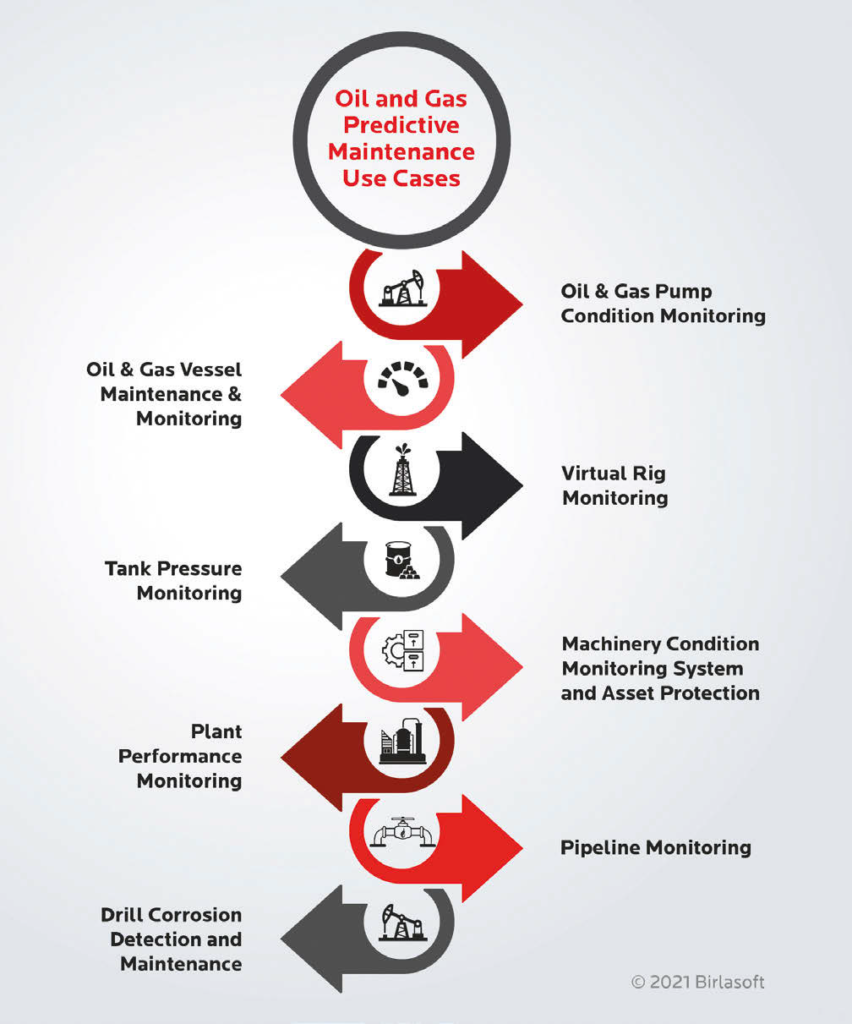
Key Components of Predictive Maintenance for Pipelines
Implementing predictive maintenance for pipelines involves several key components, each contributing to the overall effectiveness of the strategy.
- Condition Monitoring: Continuous monitoring of pipeline conditions is necessary for early fault detection. This can include techniques like vibration analysis, thermal imaging, and acoustic emission monitoring to assess the health of pipeline components.
- Data Integration: Integrating data from various sources is critical for creating accurate predictive models. This may entail combining sensor data, maintenance records, environmental factors, and operational parameters to gain a comprehensive understanding of pipeline health.
- Risk Assessment: Prioritizing maintenance activities based on risk assessment helps allocate resources efficiently. By evaluating factors such as asset criticality, failure consequences, and likelihood of failure, pipeline operators can focus on areas with the highest impact.
Predictive Maintenance measures specific to Pipeline Bolting:
- Flange Integrity Monitoring: Utilizing methods like Ultrasonic Bolt Load Measurement and Thermal Imaging to monitor the condition of flange connections continuously.
- Bolt Stress Analysis: Utilizing advanced modelling and simulation techniques to analyze the stress distribution on bolts within pipeline flange connections.
- Corrosion Monitoring: Implementing corrosion monitoring sensors directly on bolt surfaces or within proximity to assess the extent of corrosion on bolt threads or heads
- Gasket Compression Monitoring: Monitoring the compression and seating of gaskets within flange connections to ensure proper sealing integrity.
- Joint Alignment Monitoring: Monitoring the alignment of flange joints to ensure proper mating and distribution of bolt loads. Misalignment can lead to uneven stress distribution, bolt fatigue, and compromised sealing integrity.
- Bolt Load Verification: Employing load monitoring techniques, such as ultrasonic measurement or strain gauges, to verify the preload or tension in bolts used in critical pipeline connections.
Tritorc TSL Series Hydraulic Square Drive
Enhance Predictive Maintenance with Our Innovative Solutions:
- Torque Wrenches: Precision-engineered torque wrenches are essential tools for accurately tightening bolts within pipeline flange connections
- Hydraulic Bolt Tensioner: Hydraulic bolt tensioners provide controlled and uniform bolt tensioning, eliminating inconsistencies and reducing the risk of bolt fatigue or loosening.
- In-Situ Machining: In-situ machining solutions enable on-site machining of flange surfaces, ensuring precise alignment and sealing integrity.
- Tube Tools: Tube tools are specifically designed for maintenance tasks such as tube cleaning, cutting, and installation, ensuring optimal performance and reliability of your pipeline systems.
- Flange Alignment Accessories: Flange alignment accessories help ensure proper alignment and mating of flange joints, minimizing the risk of leaks and enhancing sealing integrity.
Leave a Reply