Hot Tapping or pressure tapping, is a method for connecting a branch to a “hot” or operational line. By drilling or cutting, the hot tapping procedure enables a connection into a pressurized in-service operating system. In the hot tap procedure, a branch connection and valve are attached to the exterior of an operational pipeline. The pipeline wall is then cut out within the branch, and the wall section is removed via the valve.
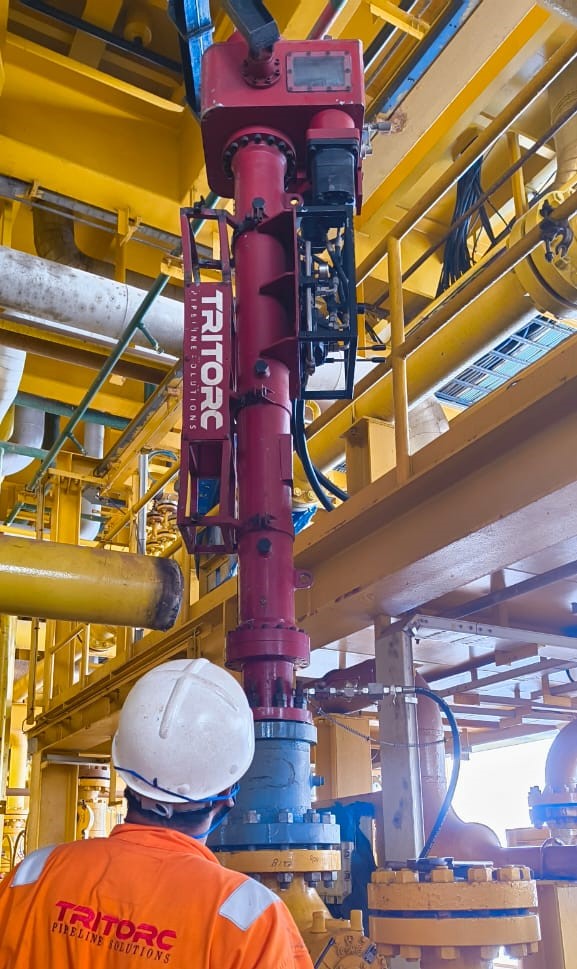
A successful Hot Tapping execution requires thorough planning and consideration of several factors to ensure safety, efficiency, and regulatory adherence. Thus, before proceeding with a Hot Tapping operation, it’s essential to carefully assess various key considerations.
Considerations before carrying out a Hot Tapping operation?
- Identification of Connection Location
- Operating pressure and temperature
- Code Compliance for Hot tapping Considerations.
[1] Selection Criteria for Hot Tapping Location:
The selection of the hot tapping location plays a crucial role in the success and safety of the hot tapping operation. A detailed inspection of the hot tap location on the run pipe shall be carried out. This process may necessitate the removal of any existing insulation or paint coating in the designated area for the hot tap. Ultrasonic examination should be conducted to assess the wall thickness and identify any imperfections. Approval for hot tapping will be granted if the location satisfies the minimum pipe wall thickness requirements and is devoid of any laminations. Excluding these there are other factors which are required to be considered in the selection criteria:
- Accessibility:
- Choosing a location that allows easy access for the hot tapping machine.
- Ensure there is sufficient space for the equipment to be installed and operated safely.
- Material Compatibility:
- Select a location where the material of the pipe is suitable for hot tapping.
- Consider the material’s thickness, composition, and integrity for successful tapping.
- Flow Considerations:
- Analyze the flow characteristics of the pipeline at the connection point.
- Ensure that the connection location does not disrupt the flow or cause pressure drops that could affect the system’s performance.
[2] Pressure and Temperature Considerations for Hot Tapping:
Maintaining a minimum flow rate within the line slated for hot tapping is crucial to dissipate heat generated during welding operations. Excessively high flow rates or velocities can result in rapid cooling of the weld, increasing the risk of cracking. Conversely, extremely low velocities can elevate pipe wall temperatures at the weld site, potentially weakening the material and heightening the risk of a blowout.
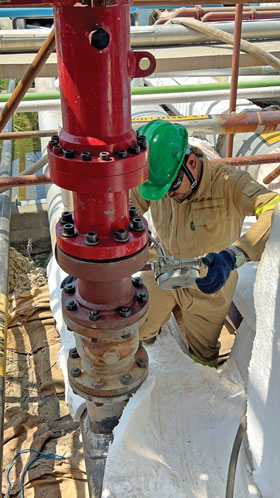
- Pressure Testing Precautions:
- Conducting pressure testing to verify the integrity of the system before hot tapping.
- Ensuring that the test pressure is within safe limits to prevent collapse of the pipe or vessel walls.
- Temperature Sensitivity:
- Consider the temperature conditions for conducting hydrostatic tests or using alternative methods like air or nitrogen testing.
- Avoid hot tapping at extreme temperatures that could affect the integrity of the metal or lead to hazardous reactions.
- Thermal Expansion Management:
- Account for thermal expansion of the contents during hot tapping to prevent overpressure.
- Implement measures to protect against thermal expansion-related issues, such as buckling or deformation of the vessel walls.
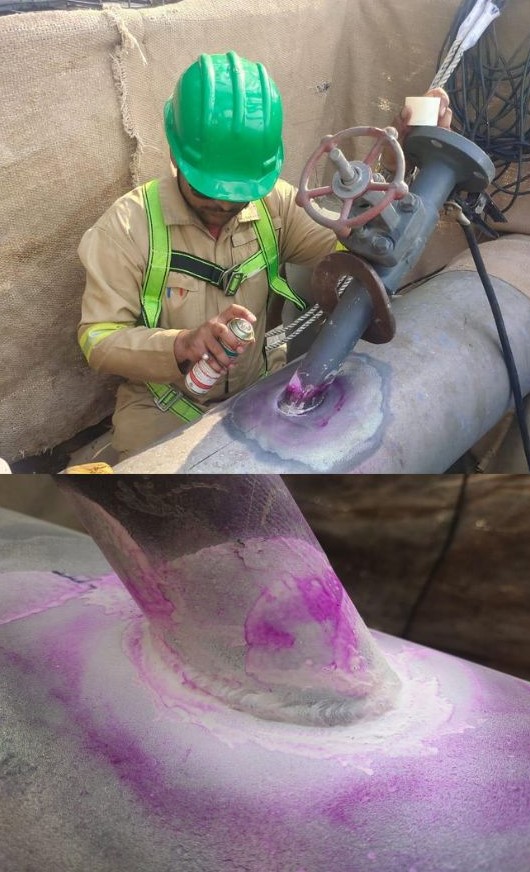
Along with all the above considerations Tritorc employs a unique Non Destructive testing method to check the surface irregularities present on the location of the pipe on which Hot Tapping is to be done. This method is called “ Dye Penetrant Test (DPT)” which is also one of the most inexpensive NDT methods.
This test method is popular by many names, which are as follows:
- Liquid Penetrant Inspection (LPI)
- Liquid Penetrant testing or Liquid Penetrant test (LPT)
- Penetrant Test or Penetrant Testing (PT)
This method can be used to inspect almost all non-porous materials such as metals, plastics, ceramics, etc. Any surface discontinuity (or irregularity) such as surface cracks, porosity, pinholes, etc. can be detected by this test method which can be helpful to qualify or disqualify a site for hot tapping operation.
[3] Code Compliance for Hot Tapping Connections:
There are several standards that apply to hot tap welding, including those related to the materials and equipment used, as well as the welding process itself. Some of the main standards that pertain to hot tap welding include
- ASME B31.3: Process Piping – This standard covers the design, construction, testing, and maintenance of process piping systems. It includes requirements for hot tap welding, such as the minimum thickness of the pipe and the maximum allowable stress for the material being used.
- API 1104: Welding of Pipelines and Related Facilities – This standard covers the welding of pipelines and related facilities in the oil and gas industry. It includes requirements for the qualification of welders and welding procedures, as well as guidelines for the design, fabrication, and inspection of welded pipelines.
- AWS D1.1: Structural Welding Code – Steel – This standard covers the welding of structural steel components, including requirements for the qualification of welders and welding procedures, as well as guidelines for the design and fabrication of welded steel structures.
- ASME IX: Welding, Brazing, and Fusing Qualifications – This standard covers the qualification of welders and welding procedures, including requirements for the testing of welders and the development of welding procedures.
At Tritorc we are capable of working in challenging conditions while following industry standard such as the following:
- API 2201 & API 1104 Appendix B
- ASME B31.3, B31.4, and B31.8
- Working with Pipes with 1450 PSIG pressure and media temperature up to 280 Deg. C
- We carry out Hot tapping on pipes with the following materials ASTM A106 GR A/B/C, API 5L X 42/46/52/56/60/65/70 and tank materials ranging from ASTM A36, A238, A285 and many more
Leave a Reply