Pipelines are a conveyance medium for various fluids that are necessary to keep civilization functional. To keep these critical pieces of infrastructure functional, several tools, accessories, and machinery are needed to keep up with the requirements of their maintenance, repair, and overhaul cycles.
Productivity is critical for maintaining profitability for the large economies of scale plants that, to provide an example: refine crude oil into various petrochemical products. Various pipeline fluid mediums such as steam, flare gas, crude oil, water, etc. require careful handling while the pipelines carrying them are drilled into and the flow is redirected to a conduit and then to its original destination.
A main pipeline called a ‘mother pipeline’ is the one that has the flowing fluid. The pipes, to which the mother pipeline could be connected are called ’branch pipelines’.
The purpose of Conducting Hot Tapping would be amongst the following:
- To remove a damaged or rusted section of pipes
- To create a conduit for the fluid to another pipeline or avoid a certain area and reconnect to the same pipeline.
The hot-tapping machine shown below has the following components:
i) Full Encirclement Fitting or Joints – usually have a pipe flange attached to them.
ii) Valve housing – Connected by bolts on the flange
iii) Tapping Machine – This is the actual element that shall perform the cutting, it has a drive component or motor that is electrically or hydraulically driven and rotates the Boring Bar that moves back and forth using a hydraulic mechanism. Here the feed and speed can be controlled.
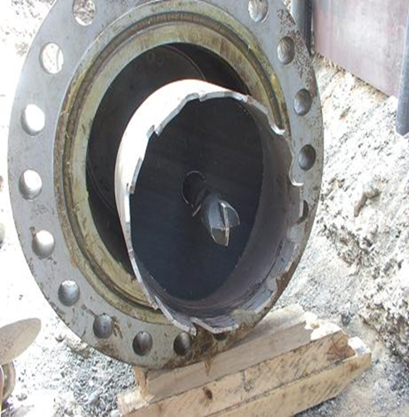
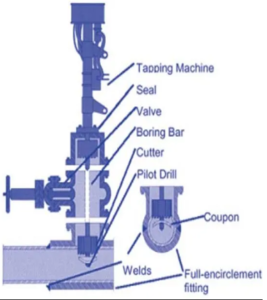
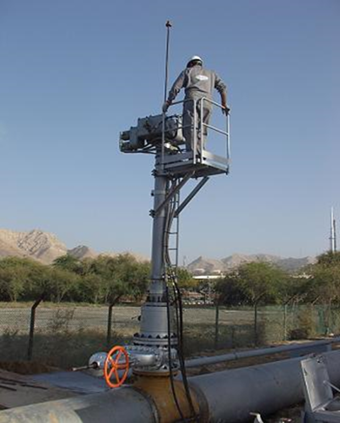
iv) Cutter – The Cutting Element has a Pilot Drill which cuts and retrieves a cut section of the pipe called a coupon with a set of prongs that stop the cut section from falling back into the pipe.
The process involves the following steps:
- Welding or Bolting the appropriate Joints on the Pipes to be hot-tapped in minimum numbers to carry out to the line stopping after hot tapping is conducted.
Examples include: Bolted or Welded Split Tee, Weld-O-Let, and Reinforcement (RF) pads
b. Bolting of the Valve housing onto the joint is carried out which shall allow the tapping machine to be mounted on the same with smaller valves being fastened on the joints and correct measurements are made for the fittings.
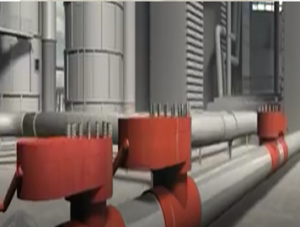
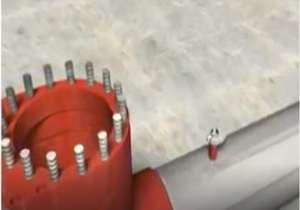
c. The Tapping Machine is mounted on the valve housing and the tapping is initiated using manual machines for the smaller taps and larger machines for the main taps
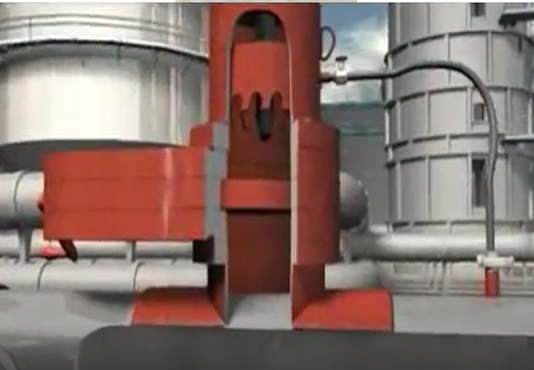
the Coupon from the Pipe and
it is secured behind the valve gate.
d. Now that both the taps are opened the pipe sections are to be connected, and the conduit is inserted and bolted on the valve housings of both, hence continuing the flow of the working fluid.
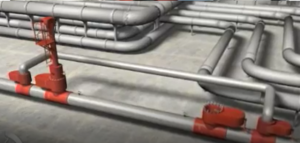
e. Further, the Line Stopping Machine is attached to the valve housing the Stopple is extended into the pipe and the flow is obstructed. In Some cases, an inflatable bag is used to stop the effervescent fumes from escaping to prevent an explosive environment or asphyxiating gasses from harming workmen or stopping their work. The excess pressure is released from the pipe which is now effectively cordoned off using line stopples.
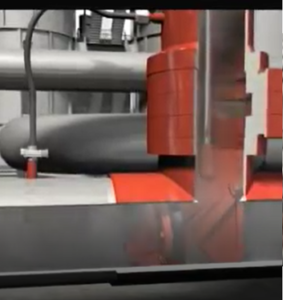
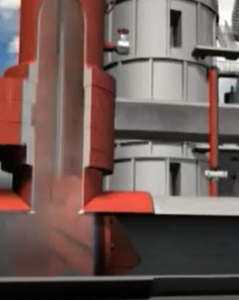
pipe section to isolated
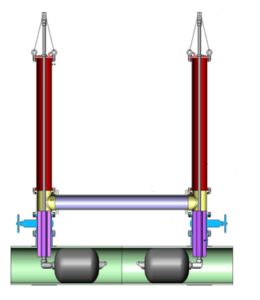
f. The Damaged or rusted section of the pipe or the desired pipeline modification is initiated
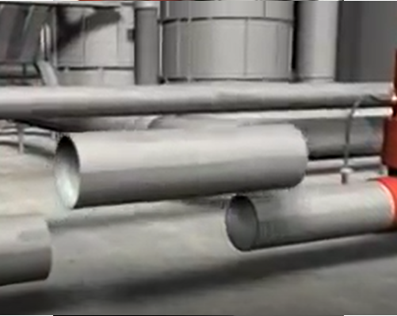
g. The Line Stopple is now Withdrawn behind the valve gate and the excess gas (if any) is released. The fluid is now free to move through the pipe and hot tapping/line stopping machines are now withdrawn.
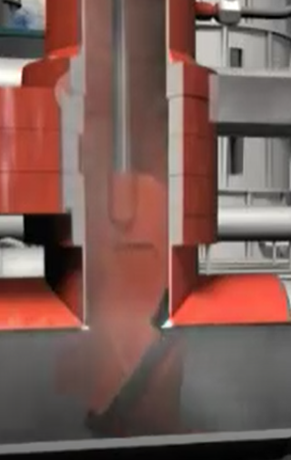
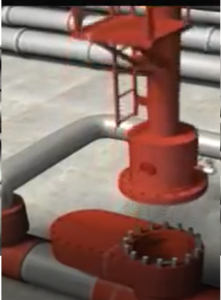
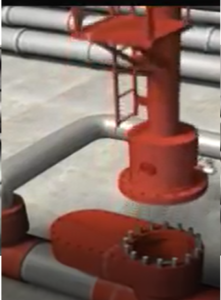
h. The Completion Flanges or blanks are now bolted and the welded fittings/joints are left in place, if the joints are bolted then they are withdrawn.
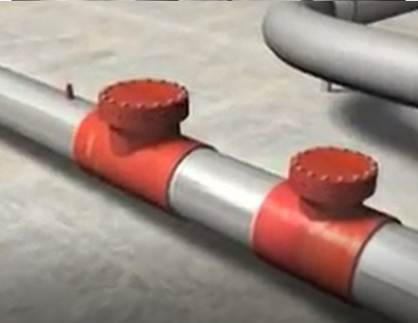
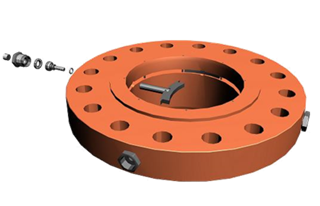
Completion Flanges are placed ensuring leakages at high pressure are unlikely
Various Orientations wherein the Hot Tapping and Line Stopping process could be carried out include the following:
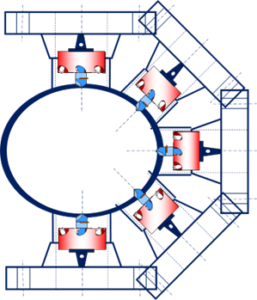
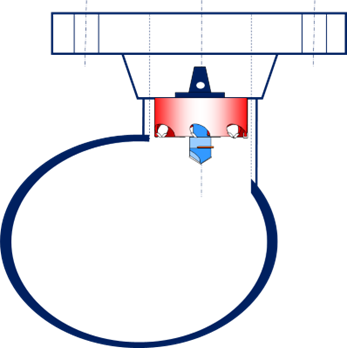
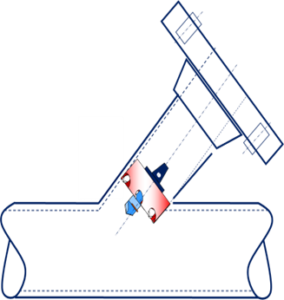
In Addition to Pipeline Hot Tapping /Line Stopping on Land, it can also be performed on Pipelines underwater.
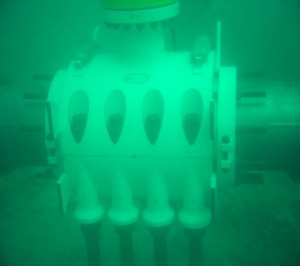
Special Underwater Sealed Valve Gates and Fittings and Joints ensure leak-free hot tapping/ line stopping material
Leave a Reply